8.3.1 总则
8.3.1.1 ●如果有规定,在计划第一次运转试验之前至少6周,卖方应向买方提交所有运转试验用的详细程序和所有规定的自选试验(8.3.4),以供买方审查和提出意见。试验程序应包括用于计算流量、扬程和功率所用的所有数据实际测量不确定度,以及验收标准。
8.3.1.2 性能试验和NPSH试验方法和不确定度的要求应按HI 14.6(ISO 9906) 1级的规定。性能容差应符合表16的规定。结果的评定应符合8.3.3.4 3。
8.3.1.3 在静水压试验过程中不应使用机械密封,但在所有运转试验或性能试验过程中应使用机械密封。
8.3.2 静水压试验
8.3.2.1 离心泵壳体静水压试验的目的是确保泵的承压部件和接合面设计和结构,在环境条件到最大工作条件下都没有泄漏。
8.3.2.2 所有承压部件应作为装配好的部件进行静水压试验。应至少在1.5倍的最大允许工作压力(MAWP)的条件下采用液体进行试验。
8.3.2.3 试验装置和/或仪器仪表不应用来改善任何整体联接的刚性。
8.3.2.4 装配好的承压壳体在静水压试验过程中所使用的垫片(不包括密封压盖)应与泵出厂时配备的垫片具有同样的设计,并且安装不应有密封剂。
8.3.2.5 试验液体的温度应高于被试材料的无塑性转变温度。
::: warning
注:更多信息参见ASTM E1003
:::
8.3.2.6 如果被试零件将在这样一个温度下运转,在此温度下,材料的强度低于测试温度下该材料的强度,则静水压试验压力应乘上一个系数,把测试温度下材料的允许工作应力除以额定运转温度下该材料的允许工作应力即可获得此系数。使用的应力值应按6.3.4的规定来确定。对于管路,如果有规定,应力值应符合ISO 15649或ASME B31.3标准。由此得到的压力应是进行静水压试验的最小压力。应记录实际静水压试验。水压试验之前应证实被试材料要求的适用性,因为在温度204℃(400℉)时,很多等级钢的性能并没有显著变化。
8.3.2.7 如果存在下列情况中的一种或多种,静水压试验液体应包含有一种润湿剂以减小表面张力:
- a) 在泵送液体温度下,泵输送液体相对密度(比重)小于0.7;
- b) 泵送温度高于260℃(500℉);
- c) 泵壳是从新模型或修改的模型铸出的;
- d) 已知此种材料的铸造流动性差。
8.3.2.8 用于试验奥氏体不锈钢材料的液体中氯化物含量不应超过100 mg/kg(100 ppm)。为了防止氯化物因蒸发干燥而沉积,在试验结束时应把所有残余液体从被试零件中清除掉。
::: warning
注:限制氯化物含量是为了防止应力腐蚀破裂。
:::
8.3.2.9 密封压盖或可移出密封腔不参与水压试验。泵壳的静水压试验不应包括机械密封。密封压盖和可移出的密封腔应按API 682的规定进行试验。与泵成一体的密封腔不考虑移开。
8.3.2.10 奥氏体、双相钢或超级双相不锈钢承压壳体可可以在去皮(粗)加工条件下进行静水压试验,见8.2.2.3。静水压试验之后再做机械加工的任何部位,都应在静水压试验报告中注明。
::: tip
注:由于最终的液体淬火引起的残余应力和此类材料固有的相对较低的比例极限,在静水压试验过程中,重要的尺寸上可能产生少量的永久变形。在静水压试验过程中,这些重要部位允许保留少量加工余量,以避免在水压试验后需要通过焊接来增加厚度来恢复公差要求严格的尺寸。
:::
8.3.2.11 试验应持续足够长时间,以允许在压力状态下对零件进行全面检查。如果在30 min内,承压零件和接合面即没有泄漏也没有渗漏,应认为静水压试验合格。对于大型和重型承压零件,可以由买方和卖方共同商定的更长试验时间。通过内部隔板的渗漏是允许的,这种隔板是试验需要的分段壳体,用来使所试验泵保持压力。
8.3.2.12 双壳体泵、卧式多级泵、一体齿轮箱泵(如6.3.8中所述)、经买方同意其他的特殊设计泵可分段地进行试验。通过内部隔板的渗漏是允许的,这种隔板是试验需要的分段壳体,用来使试验泵保持压力。如果批准在不同压力下试验分段壳体,每段应单独在适用的压力下进行试验。或对这些分段可以用合适的压力进行组合试验。
8.3.2.13 焊接的管路系统应进行静水压试验。试验及应力等级应符合ISO ASME B31.3。
::: tip
注:用管子件或螺纹接口组装的管路系统,组装后没有必要做静水压试验。
:::
8.3.2.14 除非另有规定,径向接合面直径(垫片平均直径)小于等于610 mm(24 in)的单级悬臂泵壳体部件可作为部件或分组件做静水压试验,这些部件或分组件的接合面设计完整性已经由特定规格和额定压力泵的试验证明是合格的。
8.3.2.15 冷却水通道和部件,包括轴承冷却水夹套、密封腔、油冷却器和密封冷却器,水压试验压力应至少1 000 kPa(10 bar;150 psi)的压力。
8.3.2.16 蒸汽、冷却水和润滑油管路,如果是焊接的制造,应以1.5倍的最大工作压力或1 050 kPa(10.5 bar;150 psi)压力进行试验,两者中取较大者。
8.3.3 性能试验
8.3.3.1 除非另有规定,除本文件附加要求外,每台泵都应按H14.6或ISO 9906进行性能试验。
8.3.3.2 当泵在试验台上运转时和性能试验进行之前应满足下列要求。
8.3.3.2.1 泵在做性能试验时应采用合同规定的密封和轴承。
8.3.3.2.2 泵在进行性能试验期间的任何阶段,单个密封(或多密封)泄漏量不应有超出API 682规定的泄漏量或买方与卖方共同商定的泄漏量。在泵进行性能试验期间,出现任何不允许的泄漏都需要拆卸和维修密封。如果拆开或者卸下密封,则应按8.3.3.8.4中定义的准则,将密封安装在泵上应重新进行一次气密性试验。当泵在试验台上用水试验时,适用于以水进行试验的湿式密封应没有可见泄漏。
::: warning
注:可以根据API 682的规定来审核,以证实无可见泄漏标准适合于正在进行试验的密封。值得注意的是带有高压力隔离液[大于4 000 kPa(40 bar;600 psi)]的有压双端面密封容易出可见现的泄漏。
:::
8.3.3.2.3 所有润滑油压力、黏度和温度应在运行值范围之内,这些运行值在买方操作指南中针对指定试验机组有推。
8.3.3.2.4 规定用纯油雾系统作为正常润滑的轴承,在进行性能试验之前,应采用一种合适的烃类油来进行预润滑。
8.3.3.2.5 所有接合面和接口应检查其密封性能,应消除任何泄漏。
8.3.3.2.6 应检查试验过程中使用的所有报警、保护和控制装置,并应根据要求做好调整。
8.3.3.2.7 进行性能试验的水温应不大于55℃(130℉)。
8.3.3.3 下列试验选项要求得到买方批准。
8.3.3.3.1 如果经买方批准,为了防止损坏合同密封或者合同密封与试验液体不相匹配,性能试验过程中可使用代用密封。见API 682。
8.3.3.3.2 如果有规定,试验过程中密封的泄漏,应要求组装泵和密封并再运转,以证明密封性能符合要求。
8.3.3.3.3 如果经买方批准,性能试验可以在温度大于55(130℉)条件下进行。
8.3.3.4 除非另有规定,性能试验应按下列规定进行。
8.3.3.4.1 卖方应获得足够数量点的试验数据来绘出性能曲线,数据包括扬程、流量、功率和振动等。在泵允许工作区范围内,相邻的两个流量点之间的间距不能大于额定流量的35%。图M.4给出了这些流量点的说明。正常情况下,应包括下列流量点(可以有±3%的流量偏差):
1) 关死点(振动数据没有要求);
2) 最小连续稳定流量点(允许工作区起点);
3) 最小连续稳定流量点与最佳工作区最小流量点之间的接近两者中间的流量点;
4) 最佳工作区最小流量点;
5) 最佳工作区最小流量点与额定流量之间的接近两者中间的流量点;
6) 额定流量点的95%与99%之间的之间流量点;
7) 额定流量点与额定流量点的105%之间的流量点;
8) 最优工作取最大流量点。;
9) 允许工作区终点(如果与最佳工作区终点不同)。
对于BEP 小于11 m3/h(50 gpm), 不要求3)和5)的流量点。
::: tip
注:根据曲线和额定点到BEP 的相对位置,对于给定的试验,不必记录上述所有的点。上述35%最大间隔原则,其目的是充分明确说明曲线的形状。
:::
8.3.3.4.2 一些高能泵(如一体齿轮箱泵或多级泵),在关死点试验表现出大的温升率,使得在关死点试验时,这些泵不可行和/或不安全。温升与能量密度直接相关。能量密度PD 可以近似表达:
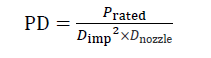
::: warning
式中:
𝑃rated——每级的额定水功率,单位MW(hp);
𝐷imp——额定叶轮直径,单位m(in);
𝐷nozzle——排出口公称直径,对于双吸、单级泵是进口法兰直径,单位m(in)。
:::
典型的PD 临界值为13 MW/m3(0.286 hp/in3),超出此值,在泵性能试验时建议泵不要在关死点运行。
8.3.3.4.3 对扬程和功率的试验数据,应使用最小二乘法,将试验数据拟合成样条曲线或适当的多项式(通常是不低于3 阶)。各流量点代入到结果多项式方程中,计算出扬程值和功率值。这些值应根据速度、粘度和密度(比重)给予修正。扬程和功率的修正值应在表16 允许的容差范围内。
==表16 性能容差 d e==

8.3.3.4.4 除非另有商定,试验转速变化应在泵试验数据表(见附录N中示例)中所列额定转速的3%以内。试验结果应修正到额定转速。
8.3.3.4.5 卖方应保留一套完整的、详尽的所有最终试验记录,并应准备好需要的份数、经确认无误的副本。资料应包括试验曲线、试验性能数据与保证点比较的一览表(见L.2.4,L.3.2.2和附录M中的示例)。
4.3.3.4.5 ●如果有规定,除了按L.3.2.2的规定正式提交最终资料外,发货之前,在完成性能试验的24h之内,应把曲线和试验数据(根据转速、比转数和粘度修正的)提交买方做技术审查和验收。
8.3.3.5 ●对于大功率泵[>1 MW(1350 hp)),表16 以外的性能容差可能是合适的。如果有规定,泵在额定流量点的效率应限定在买方给出容差之内,并且应包含在泵额定性能范围内。如果对额定效率规定了容差,应在靠近实际额定流量点处取附加试验点。额定效率和容差应符合所采用的试验规范,特别需要注意的是,要根据试验规确定效率不确定度。
8.3.3.6 在性能试验过程中,应满足下列要求。
8.3.3.6.1 应按6.9.4.2的要求和规定的试验点记录振动值。振动值不应超出6.9.4.6中的给定值。
8.3.3.6.2 对于油环和溅油润滑系统,在试验的开始和结束时,应记录油温度。对于纯油雾润滑系统,应记录试验开始和结束时的轴承箱温度。对于强制润滑系统,应记录试验开始和结束时的轴承金属温度。在试验报告中应注明试验的持续时间。
8.3.3.6.3 泵应在6.10.2.7规定的轴承温度限定值内运行,不应出现出不良的运转迹象,例如由于汽蚀引起的噪声。
8.3.3.6.4 如果泵在额定转速运行,泵的性能容差应在表16给出的范围内。
8.3.3.6.5 泵运行时应没有可见的润滑油泄漏。
8.3.3.7 ●如果有规定,性能试验应在试验装置上进行,试验时的NPSHA值应不大于买方规定的NPSHA的110%。
::: warning
注:这样试验的目的是评估泵入口在规定的NPSHA条件下泵的性能。
:::
8.3.3.8 完成性能试验之后,应满足下列要求。
8.3.3.8.1 为了车削叶轮来满足扬程容差,需要在性能试验后拆卸泵,如果叶轮直径车削量不超过原来直径的5%,则不需要重新试验。工厂试验时的叶轮直径和最终的叶轮直径都应记录在工厂验证的试验曲线上,并给出叶轮直径切割后的运转特性曲线。
8.3.3.8.2 ●如果有规定,在多级泵试验之后,解体进行任何的扬程调整(包括小于5%叶轮直接弄个的变化)都应重新试验。
8.3.3.8.3 如果由于其他修正项目(如水力性能、NPSH或机械运转)需要拆卸泵,最初的试验不应验收;在完成这些维修项目之后,应进行最终的性能试验。
8.3.3.8.4 如果在性能试验之后需要拆下机械密封部件,或要用工作密封面更换试验密封面,则最终的密封部件应按下列程序规定进行气密性试验试验。
- a) 对每个密封段单独用清洁的空气加压到172 kPa(1.72 bar;25 psi)的试验压力;
- b) 把试验装置与压力源隔离开,并且保持压力至少5 min,或者每30 L(1 ft3)试验容积保持压力5 min,两者中
取较大值;
- c) 试验过程中允许的最大压力降应是14 kPa(0.14bar;2 psi)。
8.3.3.9 ●除非另有规定,最终性能试验后不应拆卸泵。泵包括密封腔应排放到一定程度,在试验后的4h内灌满置换水的抑制剂并排放干净。对有些泵型,如BB3和BB5,如果采用这个方法水不能被置换,泵应做更多的必要的拆卸,以确保在使用缓冲剂之前将所有水从内部流道、平衡管中排尽,以防止腐蚀和冻裂的可能。
注:在最终性能试验后,进行泵的拆卸对机组的机械完整性有影响,这点在试验中得到了证明。流体动压轴承的检查可以轻松完成,并且影响也是最小的。滚动轴承的检查仅限于打开轴承端外侧的压盖(如果有的话)。对于所有泵型,拆除轴承内侧压盖要需要考虑更多的拆卸,对OH和VS型泵意味着完全拆卸。对于所有泵型,泵内部检查需要拆卸泵体的连接件、BB型和VS型泵机械密封、BB2和BB5型泵的驱动端轴承。
8.3.4 可选试验
8.3.4.1 总则
●如果有规定,应进行8.3.4.2~8.3.4.7中所述的工厂试验。在进行试验前,买方和卖方应共同商定试验细节和要求的数据(如振动和温度数据)。
8.3.4.2 机械运转试验
8.3.4.2.1 ●如果有规定,泵应在试验台上运转,在额定流量下测量和记录轴承油温。试验应连续运转到油温测量稳定,即:10 分钟内油温上升相对环境温度不超过1℃(2℉)。
8.3.4.2.2 ●如果有规定,泵应在额定流量下进行机械运转4 h。
8.3.4.3 必需汽蚀余量试验
8.3.4.3.1 ●如果有规定,除本文件附加要求外,泵应按HI 14.6或ISO 9906的规定进行必需汽蚀余量试验试验。
8.3.4.3.2 必需汽蚀余量试验应测定8.3.3.4.1规定的2、5、6、7、和8点的NPSH3值,就是基于扬程(两级或多级泵的第1级扬程)下降3%时的汽蚀余量。如果可能的话,两级或多级泵的第一级扬程应在第一级排出部分用单独的接口来测量。或者应只试验第1级。只有经买方批准,第一级扬程可用总扬程除以级数来确定。
8.3.4.3.3 除非另有规定或商定,必需汽蚀余量试验应是在每一个试验点上进行,每个试验点都保持恒定的流量,通过逐渐降低NPSHA记录扬程和NPSHA测量数据,直到扬程下降超过了第一扬程值的3%(HI14.6 第2类汽蚀试验)。扬程下降值超过20%(对于多级泵是第1级扬程的20%)不应继续试验。
8.3.4.3.4 对于必需汽蚀余量试验的每个试验点,第一扬程值应是开始试验的NPSHA条件下测量的;开始试验的NPSHA至少等于报价单曲线上对应流量点的NPSH3 值的两倍;如果该值太大,开始试验的NPSHA值等于在对应流量点泵性能试验提供的NPSHA值。
::: warning
注:如果按8.3.3.7规定的性能试验要求,扬程可能已经受到NPSHA不足的影响,那么 用一个较高的NPSHA开始试验是可取的。
:::
8.3.4.3.5 对于必需汽蚀余量试验的每个试验点,通过将泵NPSHA减少至少1m,测定的第二扬程值与第一扬程值的差值,应不大于试验所用压差测量装置测得的压差允许合成不确定度。 如果两者差值大于压差允许不确定,试验开始的NPASHA就应提高,再重复试验进行两者的比较,直至两扬程差值达到容差。
8.3.4.3.6 一组H-NPSHA数据就是必需汽蚀余量试验的每一个试验点结果,多组H-NPSHA数据应单独记录并分别绘制H-NPSHA曲线。在这些曲线上应分别标示出获得每个试验点NPSH3值。另外,按据HI 14.6或ISO 9906的要求,应采用NPSH3-Q曲线来记录必需汽蚀余量试验结果。
8.3.4.3.7 额定点NPSH3值容差不应超过限定值(见表16)。为修正NPSH3性能所进行的拆卸需要重进行性能试验和必需汽蚀余量试验。
8.3.4.4 机组试验
8.4.3.4.4.1 ●如果有规定,泵、驱动机组和包括组成机组的所有辅助设备应一起进行试验。如果有规定,应进行扭转振动测量来验证卖方的分析。应做整体机组试验以代替独立部件的单独试验,或代替除买方规定的独立部件外的单独试验。
8.3.4.4.2 机组各部件可接受的振动验收极限应按照各自的验收标准和规范的规定,往复式发动机除外(这种情况下,限值应由买方、泵供方和发动机的供方共同商定)。
8.3.4.5 ●声级试验
如果有规定,声级试验应按买方和卖方的协定进行。
::: tip
注:ISO 3740、ISO 3744 和 ISO 3746可考虑作为依据。
:::
8.3.4.6 ●辅助设备试验
如果有规定进行共振试验,在泵未接管的情况下,用撞击或其他合适的方法来激振轴承箱,用快速傅里叶变换(FFT)频谱测量确定固有频率模态,并应符合下列8.3.4.7.1~8.3.7.4规定的要求.
8.3.4.7.1 应记录和储存数据。
8.3.4.7.2 在固有频率模态和下列激振频率之间应存在一个间隔裕量:
- a) 转速的倍数,转速单位为转每分钟( r/min):1.0;2.0;3.0;
- b) 叶片通过频率的倍数:1.0;2.0。
8.3.4.7.3 试验的验收标准应由买方和卖方共同商定。在轴承箱共振条件不能改变情况下,轴承箱(组)和其附件的动力学特征的接受性,应通过轴承箱定期性能试验的振动测量来证明。如果轴承箱振动水平超出了6.9.4.6规定的最大允许值,应通过减少叶片通过的激振水平来改进。
8.3.4.7.4 在调速驱动应用中,买方应规定适用的连续工作转速范围。
::: warning
注:上述原则适用于定速泵工作。关于调速驱动应用,由于潜在的较大工作转速范围,通常不可能满足所有适用频率的间隔裕量要求。这种情况的接受性可以通过在变速性能试验中的振动测量来证明(如适用)。如果无法证明接受性,买方和卖方应协商进一步测量,旨在降低叶片通过激振水平。在调速驱动领域,可以通过编程避免在一个特定的较小的工作转速范围内连续运行。值得指出的是,由于减小了泵的能量级,在较低运行转速下共振条件没有像较高速度下共振条件那样重要。
:::
8.3.4.8 ●备件试验
如果有规定,转子、联轴器、齿轮箱、隔板、轴承和机械密封等备件应进行试验。卖方应确保这些备件可以与原配设备同时进行试验,并提供所有必需的备件。买方和卖方应共同商定试验程序。