8.2.1 总则
8.2.1.1 ●卖方应将下列资料至少保留20年:
- a) 必需的或规定的材料证明书,如工厂试验报告;
- b) 证明已经满足技术规范要求的试验数据和结果;
- c) 如果有规定,所有修理详情和作为修理程序一部分而进行的所有热处理记录;
- d) 质量控制试验和检查结果;
- e) 完工的运转间隙;
- f) 买方规定或适用的规范或规程(见L.3.1和L.3.2)所要求的其他资料。
8.2.1.2 承内压的零部件,在完成规定的检查和试验项目之前不得涂漆。
8.2.1.3 ●除6.12.1.6的要求外,买方可规定下列内容:
- a) 零件应进行表面检查和近表面检查;
- b) 要求检查的形式,如磁粉检测(MT)、液体渗透检测(PT)、射线波检测(RT)和超声波检测(UT)。
8.2.1.4 在买方最终检查之前,所有的初步运转试验和机械检查应由卖方完成。
8.2.2 压力泵壳和流程管路材料检查
8.2.2.1 除非另有规定,承压壳体和流程管路的材料应按表14中所列的要求进行检查。
::: tip
注:尽管设计的泵要满足规定压力和温度的要求,并且壳体按照本文件的要求进行静水压试验,这本身并不能保证材料在应用中具有合适的质量。材料加工过程的重要变化可以影响铸件质量。材料标准(如ASTM)对材料本身提出了最低要求,但是铸件可能受制于缩孔面积、气体孔隙度、热裂、砂夹杂物、焊接修补不当等因素的影响。此外,一些容易产生晶界撕裂或裂纹的材料,由温度、压力、振动和管道变形等引起的在役应力作用下,可能加剧晶界撕裂或裂纹。
:::
8.2.2.2 对于双壳体泵,外壳体的压力/温度应用来确定外壳体的检验等级(见8.2.2.1)。内壳体应按Ⅰ级检验(表14)。
==表14 承压壳体材料检验要求==
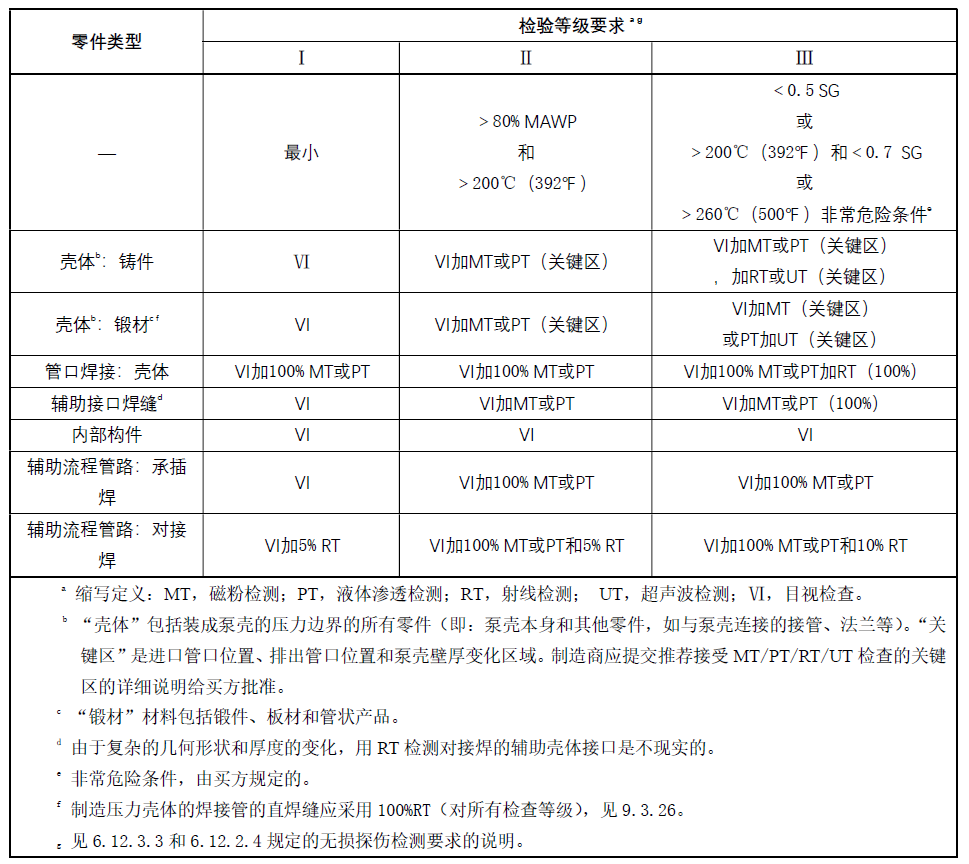
8.2.2.3 应按下列时间节点进行表14规定的检查。
8.2.2.3.1 目视检查/磁粉检测/液体渗透检测应在去皮(粗)加工以及最终热处理后进行。在去皮(粗)加工条件下,需要加工的重要尺寸及所要求的公差的区域仍保留着材料的附加余量。这种附加余量(加工余量)不得超过1 mm(0.040 in),或者最小允许壁厚的5%,两者中取较小值。
8.2.2.3.2 铸件的射线检测/超声检测应在最终热处理后进行。
8.2.2.3.3 焊缝的RT、锻件材料和焊缝的超声检测均应在最终热处理后进行。锻件材料的超声检测应在能影响超声检测的机械加工作业前进行。
8.2.2.4 如果铸造件的结构不能做射线检测,可用超声波检测来代替射线检测。
8.2.2.5 除非另有规定,检测方法和验收标准应按表15要求的材料技术规范执行。如果买方规定焊缝或材料要进行射线检测、超声波检测、磁粉检测或液体渗透检测,检测方法和验收标准应符合表15给出的标准。替代标准可由卖方推荐,或者由买方规定。为此,可使用附录N中的“焊接和材料检查数据表”。
==表15 材料检查标准==
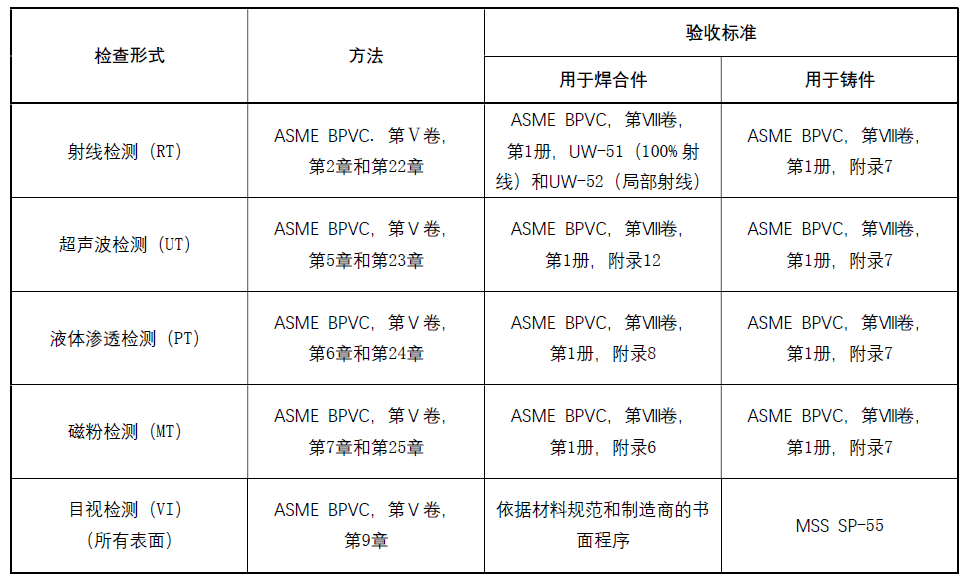
8.2.2.6 ●如果有规定,在装配之前,买方可检查由卖方或通过卖方提供的设备及所有管路和附件的清洁度。
8.2.2.7 ●如果有规定,应通过试验验证零件、焊缝及热影响区的硬度是在允许值范围内。这种试验的方法、范围、文件要求及见证应由买方和卖方共同商定。
8.2.2.8 ●如果有规定,合金材料的承压零件应采用公认的试验方法、仪器仪表和标准进行材料可靠性鉴定(PMI)。买方和卖方应共同商定要做试验的特殊零件、所采用的程序和验收标准。应使用能提供定量结果的技术。工厂试验报告、材料成份证明书、可见的标记或标识不应用来替代PMI试验。
::: warning
注:PMI是不能用来区分碳钢材料等级的。
:::