6.9.1 总则
6.9.1.1 第9章的每种特定泵型都涵盖了临界转速和横向分析的专题。
6.9.1.2 单级级和两级泵的转子应设计成第一阶干态弯曲临界转速至少大于泵最大连续运转速度的20%。
6.9.1.3 为了获得满意的密封性能,具有最大叶轮直径,并且在规定转速和规定液体条件下运行的泵,在允许工作范围的最苛刻动力学条件下,轴刚性应将主密封面处的总挠度限制到50 μm(0.002 in)以内。轴挠度的限制可结合轴径、轴跨距或悬臂以及壳体设计(包括使用双壳体或导叶)来实现。对于单级泵和两级泵,不考虑叶轮耐磨环处液膜刚度影响。对于多级泵,耐磨环、产品液体润滑轴承和轴承衬套的液膜刚度应按1倍和2倍公称设计间隙进行计算。
6.9.2 扭转分析
6.9.2.1 应采用图29的流程来确定扭转分析。除非轴系包括液力耦合器,否则分析应是整个轴系。在所有情况下,负有机组责任的卖方应有责任指导任何必要的改动,以满足6.9.2.3~6.9.2.9的要求。
注:泵通常进行三种一般形式的扭转分析:
- a) 无阻尼固有频率分析:确定机组扭转固有频率和相应模态,形成Campbell 图,以确定潜在的共振点;
- b) 稳态强迫响应分析:应用稳态激励源(如动态扭矩函数)进行谐波响应分析,计算出动态扭矩和应力来评价机械整体性;
- c) 瞬态强迫响应分析:应用瞬态激励源(如电动机启动和短路事件)进行转子强迫响应分析,计算出动态扭矩和应力来评价机械整体性。
6.9.2.2 如果机组是下列情况之一时,负有机组责任的制造商应进行无阻尼固有频率分析:
- a) 机组由三个或更多的耦合机器组成,额定功率不小于1 500 kW(2 000 hp);
- b) 感应电动机或透平通过齿轮连接,额定功率不小于1 500 kW(2 000 hp);
- c) 内燃机,额定功率不小于250 kW(335 hp);
- d) 同步电动机,额定功率不小于500 kW(670 hp);
- e) 调速驱动(ASD)的变频电动机,额定功率不小于1 000 kW(1 350 hp);
- f) 带驱动机的立式泵,额定功率不小于750 kW(1 000 hp);
- g) 感应(异步)电机的机组,额定功率不小于1 500 kW(2 000 hp)。
::: warning
注1:一些制造商的经验是立式泵,特别是带长轴的立式泵和驱动机转子有相对大的惯性,很容易受到非常小的扭转激励的影响。
注2:多数现代变频驱动(VFD),如果运行正常,只会产生很小的扭转振动和轴应力。 变频驱动(VFD)的故障可能会产生显著的激励。产生明显的扭转脉动的某些设计依然存在。
:::
6.9.2.3 如果有规定,对于变频驱动(VFD),应进行稳态强迫响应分析。这种分析应考虑12 倍电网频率以内的所有响应频率。
6.9.2.4 如果有规定或同步电动机额定功率不小于500 kW(670 hp)时,应进行瞬态强迫响应分析。如果进行,瞬态时域分析应满足6.9.2.10~6.9.2.13的要求。
::: warning
注:如果认为发电机相间故障或单相接地故障是一个重大风险,或者失去动力时发生快速总线切换,一些买方会选择进行瞬态强迫响应分析。
:::
==图29 扭转分析流程图==
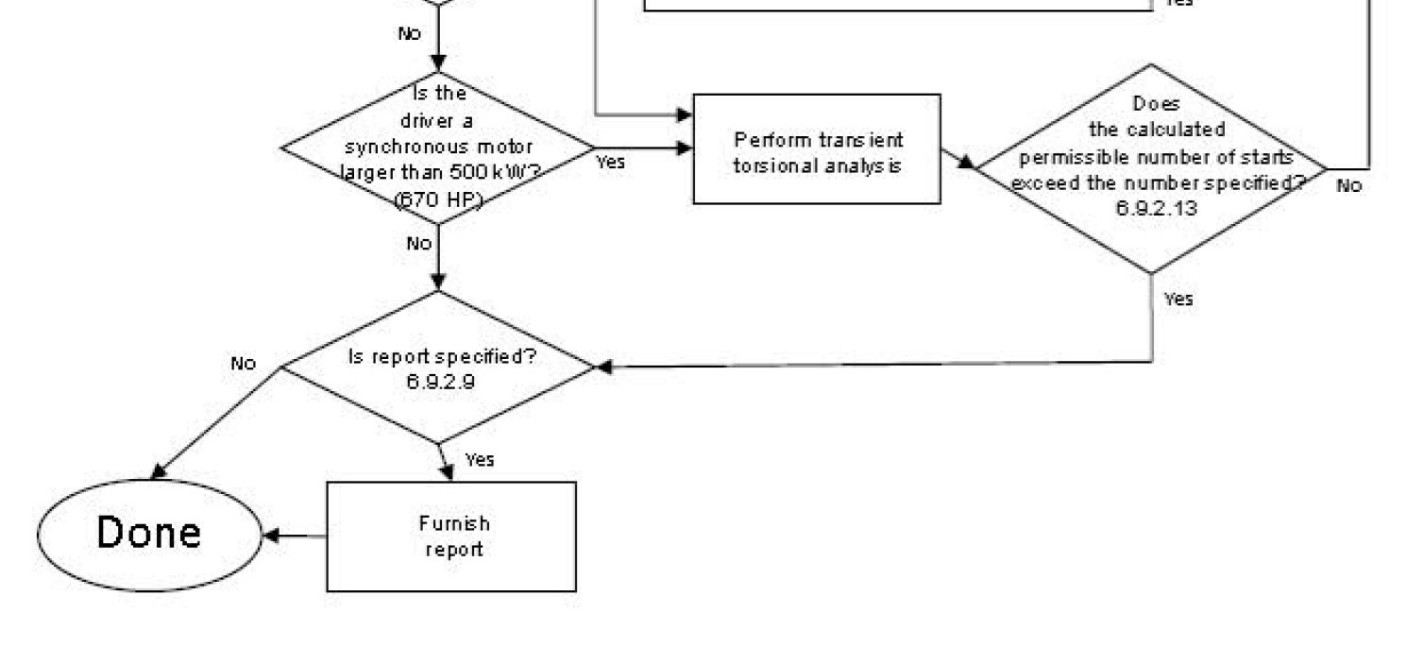
6.9.2.5 扭转固有频率激励可能有很多激励源,它可能是也可能不是转速的函数,宜在分析中加以考虑。激励源可以包括但不限于以下所列:
- a) 泵和液力透平:1 倍和2 倍转子转速,叶轮叶片和隔舌的通过频率;
- b) 齿轮:啮合频率;
- c) 感应电机:1 倍和2 倍转子转速,1 和2 倍电网频率;
- d) 2 冲程内燃机:n 倍转子转速,n 是每转动力冲程数;
- e) 4 冲程内燃机:n 和0.5 倍转子转速,n 是每转动力冲程数;
- f) 同步电动机:n 倍滑差频率(仅瞬态现象),1 和2 倍电网频率;
- g) 变频驱动:n 倍转子转速[(单位为转每分钟(r/min)],12 倍电网频率内的相关倍数,其中n 是电机极数;
::: warning
注:对于VFD 机组扭矩分析,VFD 转矩响应令人关注。这些取决于负载的转矩函数通常由驱动机制造商给出。
:::
6.9.2.6 在规定工作转速(从最小连续转速到最大连续转速)范围内,整个机组的扭转固有频率应至少比任何可能的激励频率高10%或低10%(9.6.2.5中列出)。如果固有频率不变,表明没有不利影响。
6.9.2.7 如果扭转共振计算结果落在6.9.2.6(并且买方和卖方都同意,为使共振点离开限定的频率范围已经竭尽全力的)规定的频率间隔范围内,应进行稳态响应分析,以证明共振对整个机组没有不利影响。在分析中关于激励幅度和阻尼程度的假设应清晰地标明。买方和卖方应共同商定扭转分析的验收准则。
::: warning
注:稳定强迫响应扭转分析已经表明,在VFD激励响应条件下,脉宽调制驱动的泵有令人满意的低应力;对机组没有不利的影响。
:::
6.9.2.8 除非另有规定,如果仅进行稳态无阻尼扭转分析,带有质量弹性数据表格和计算方法简要说明的Campbell图可作为报告提供给买方。
6.9.2.9 如果有规定,或者进行了稳态响应分析或瞬态强迫响应分析,制造商应提供详细的扭转分析报告。报告应包括下列内容:
- a) 机组扭转固有频率计算方法的描述;
- b) 质量弹性系统图;
- c) 质量弹性系统每个元件的质量力矩和扭转刚度的表格;
- d) Campbell 图;
- e) 提供应力峰值与每一组响应频率的模态图。
6.9.2.10 除了用于计算的参数外(如6.9.2.2规定的无阻尼扭扭转固有频率分析),瞬态强迫响应分析应包括下面内容:
- a) 电动机的平均扭矩、脉动扭矩(直轴和交轴)-转速的特性;
- b) 负载扭矩-转速的特性;
- c) 影响电动机端电压或关于端电压做出的假设(包括启动方法,如直接启动或一些降压启动方法)的电气系统特性。
6.9.2.11 强迫响应分析应得出最大扭矩,瞬态强迫响应分析应得出机组每个轴系的扭矩与时间的关系。最大扭矩应用来评估耦合部件、传动装置、过盈配合零部件(联轴器轮毂)和轴上应力集中位置的峰值扭矩能力。扭矩随时间的变化应用来对轴、键和耦合零部件进行的疲劳累积损伤分析。
6.9.2.12 应使用适当的疲劳特性和应力集中。
6.9.2.13 应采用适当的累积疲劳法则计算启动和/或停机次数的安全值。买方和卖方应共同商定安全的启停次数。
::: warning
注:采用的启动次数取决于所用的分析模型和卖方经验。正常的启动次数是1000次到1500次。API 541要求5000次启动,对电动机来说这是一个合理的假设。然而,对于被驱动的设备将要进行冗余设计才能满足这一要求。
:::
6.9.3 平衡
6.9.3.1 叶轮、平衡鼓和类似的主要转动零部件应按ISO 1940-1 G2.5级做动平衡。平衡用的芯轴质量应不大于需要做平衡部件的质量。轴不需要做平衡。对于带有过盈配合部件的BB1型和BB2型单级泵转子,卖方可以对转子部件(符合9.2.4.2)做平衡替代主要转动部件单独做平衡。
::: warning
注:ISO 21940-11标准中,不平衡是用平衡品质等级来衡量。每个ISO平衡品质等级覆盖一个不平衡范围。在本文件中 给出USC单位的名义等效限值近似等于ISO范围的中点。
:::
6.9.3.2 如果零件的D/b≥6.0(见图30),可在一个平面上做平衡。
==图1 允许单面做平衡时旋转零件尺寸的确定==
==a) 单吸叶轮== ==b) 双吸叶轮==
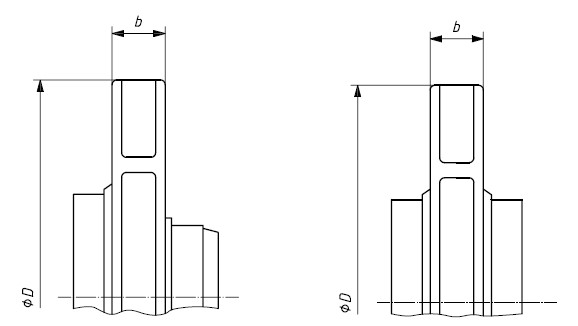
==c) 推力盘== ==d) 平衡鼓==
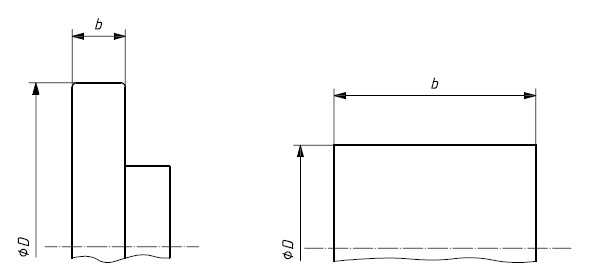
::: tip
b——宽度;
D——直径。
:::
6.9.3 转子平衡应按每种泵具体章节中的要求进行。
6.9.3.4 如果有规定,叶轮、平衡鼓和类似的转动零部件应按ISO 1940-11 G1级做动平衡。
6.9.3.5 如果有规定,叶轮、平衡鼓和类似的转动零部件动平衡应做到:
𝑈 = 4𝑊/n
::: warning
式中:
U——每个平面的不平衡量,单位为盎司-英寸(ou-in);
W——零件(部件)质量,单位为磅(lb);或每台平衡机(转子)辊颈的载荷,单位为磅(lb);
n——泵转速,单位为转每分钟(r/min)。
:::
::: tip
注:4𝑊/n是USC单位制中定义的平衡允差。使用现代的平衡机,将装在芯轴上的零部件平衡到U= 4W/n(USC单位制)或更低(取决于部件的质量),并用残余不平衡量检查来检验部件不平衡是可以做到的。由于精细的不平衡要求更微小的质量偏心距值,因此部件拆卸后再装配到平衡芯轴后, ISO G1或𝑈 = 4𝑊/n等级的动平
衡通常没有重复性。见9.2.4.2.2。
:::
6.9.4 振动
6.9.4.1 离心泵的振动随流量大小而变化,通常在最佳效率点附近最小,随着流量增大或减小而增加。偏离最佳流量点的振动随流量而变化取决于泵能量密度、比转数和汽蚀比转数。振动的变化通常随能量密度,比转数,和汽蚀比转数等因素的增加而增加。根据这些一般特性,离心泵的工作流量范围可以分成两个区域,一个为“优先工作区”,在此范围内,泵表现出低振动;另一个为“允许工作范围”,以最大流量点和最小流量点来界定,泵在此流量点上振动达到较高,但仍然是“可接受”的水平。图31解释了这一概念。振动以外的其他因素,如随着流量减小温度升高或随着流量增大NPSH3增大,也可能使得“允许工作范围”变得更窄。“允许工作范围”应在报价单中说明。如果“允许工作范围”受到振动以外的因素限制,这个因素也应在报价单中予以说明。
==图31 流量与振动关系==
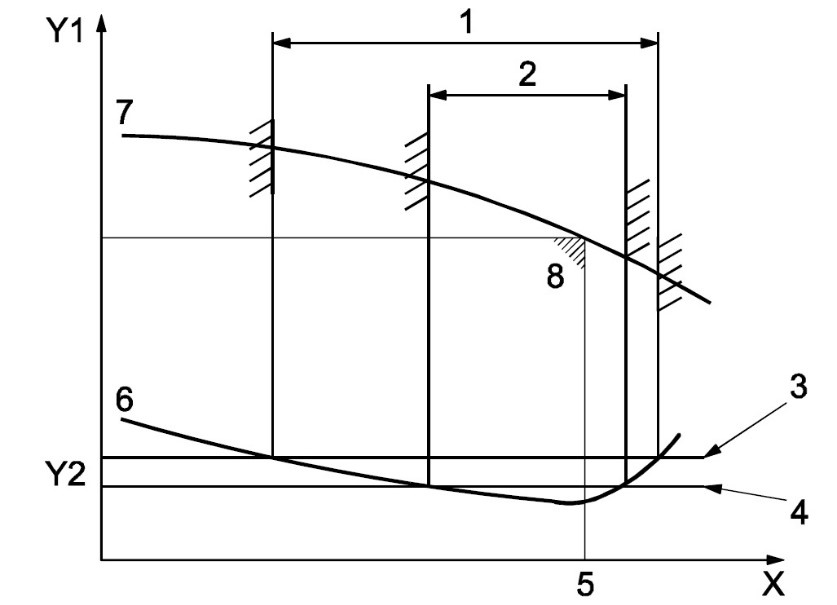
::: warning
X——流量;
Y1——扬程;
Y2——振动;
1——允许工作流量范围;
2——最佳工作流量范围;
3——流量极限内最大允许振动限制;
4——基本振动限值;
5——最佳效率点流量;
6——表明最大允许振动的典型的振动-流量曲线;
7——扬程—流量曲线;
8——以扬程和流量表示的最佳效率点。
:::
6.9.4.2 在性能试验过程中,在至少5个试验点上,5Hz到1 000 Hz范围内应进行全部振动测量,并进行快速傅里叶变换(FFT)变换得到离散振动测量的频谱。这些测量点应包括额定流量点和允许工作区和优先工作区定义的最大流量和最小流量。关死点不要求测量振动。应在下列位置进行振动测量:
- a) 各种泵的轴承箱或相应部位,位置见图32~图34(额定点振动值建议在水平和垂直平面上读取,所有其他工况点较高的振动值也在相同平面读取);
- b) 如果泵配置接近探头(非接触振动探头),要在流体动压轴承的泵轴的X 和Y 两个方向安装探头。
==图32 OH 和BB 型泵上测取振动读数的位置==
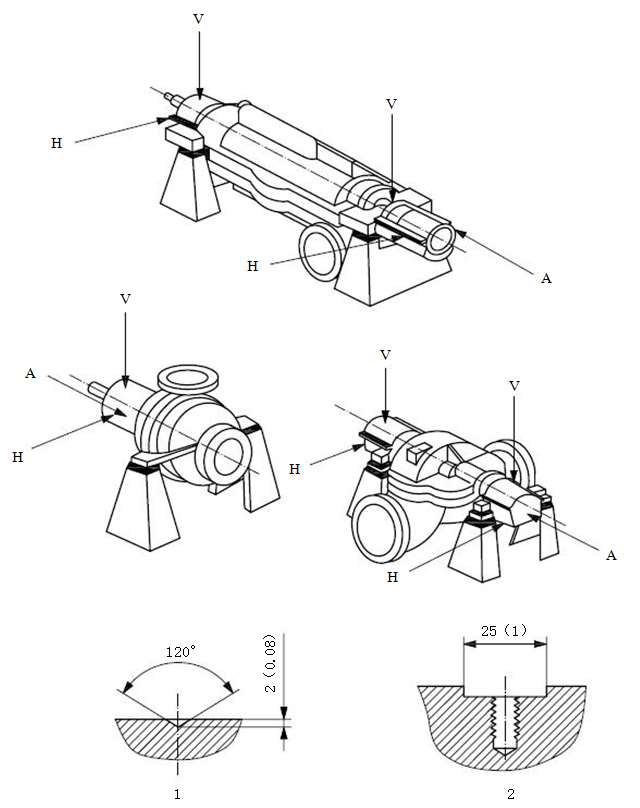
::: warning
A——轴向;
1——凹坑(见6.10.2.9);
H——水平方向;
2——安装振动测量设备的可自由选用的设施(见6.10.2.10)。
a)——垂直方向;
:::
==图33 立式悬吊(VS)泵上测取振动读数的位置==
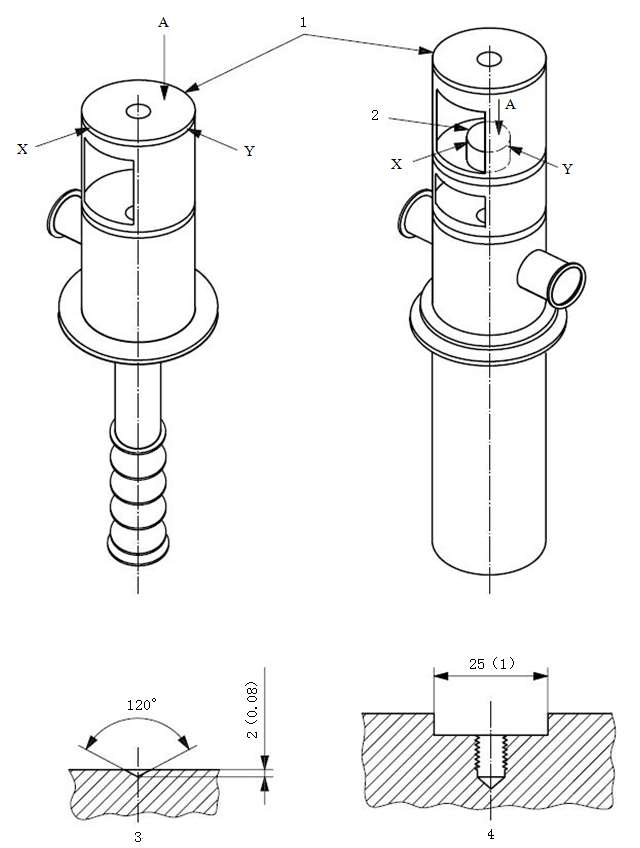
::: warning
1——驱动机安装表面;
A——轴向。
2——泵轴承箱;
3——凹坑(见6.10.2.9);
4——安装振动测量设备可自由选用的设施(见6.10.2.10);
:::
==图34 [a)]立式管道(OH3)泵和[b)]高速一体齿轮传动(OH6)泵上测取振动读数的位置==
==a)立式管道(OH3)泵 b)高速一体齿轮传动(OH6)泵==
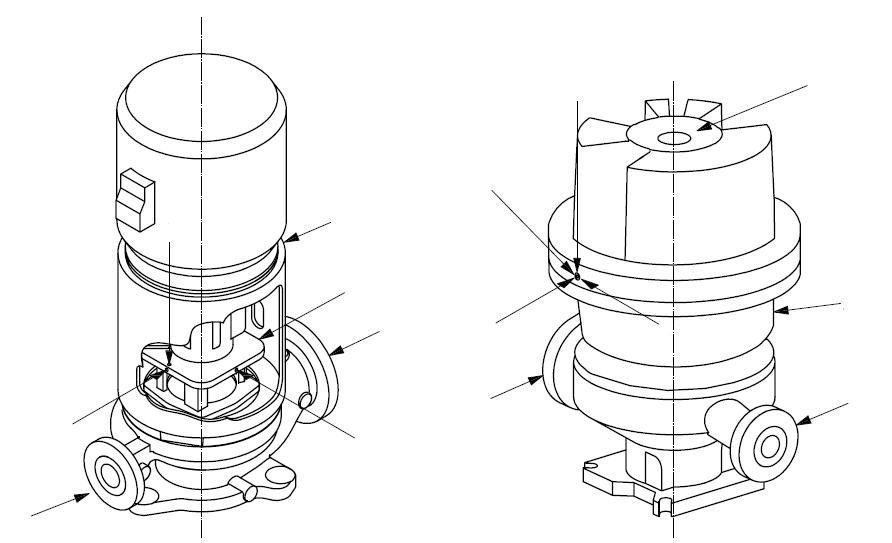
==c)凹坑(见6.10.2.9) d)安装振动测量设备的设施==

::: warning
1——驱动机安装表面;
2——泵轴承箱;
3——齿轮箱;
4— —吸入法兰;
5——排出法兰;
6——用双头螺柱安装振动传感器的螺纹接口;
A——轴向。
:::
6.9.4.3 FFT 频谱应包括从5 Hz 到2Z 倍运行转速的频率范围(这里,Z 为叶轮叶片数;在装有不同叶轮的多级泵中,Z 是任何一级叶轮的最大叶片数)。频谱图应包括在泵的试验结果中。
::: tip
注:1.0、2.0和Z倍运行转速的离散频率的振动与泵各种不同的现象有关,因此在频谱中具有特殊意义。
:::
6.9.4.4 轴承箱上所有点的测量值应采用速度均方根(RMS),单位为毫米每秒(mm/s)[英寸每秒(in/s)]。
6.9.4.5 轴上振动测量应是峰-峰位移,毫米(mm)[密尔(mils)]。
6.9.4.6 在性能试验过程中测得的振动不应超过下面给出的值:
- a) 表8用于悬臂泵和两端支承泵;
- b) 表9用于立式悬吊泵;
- c) 图35用于高能量泵。
提供接近探头的供货泵应同时满足轴承箱和轴振动限值。
::: warning
注:轴承箱上所有振动限值仅定义为RMS测量值。
:::
==表8 悬臂泵和两端支承泵的振动极限值==
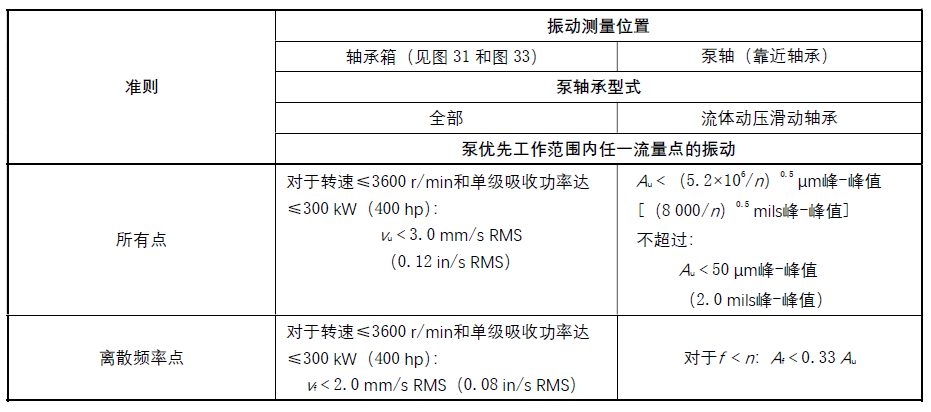
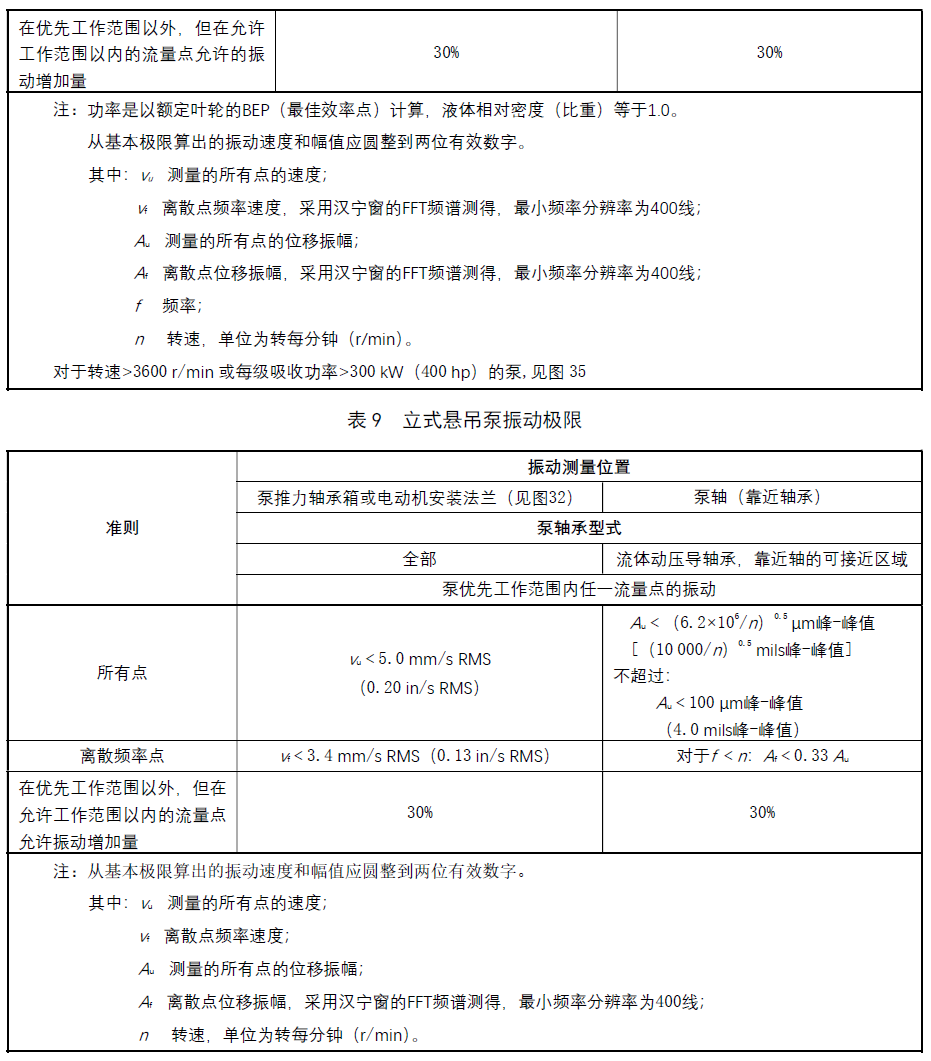
6.9.4.7 高于最大连续转速的任何转速,达到并包括驱动机的跳闸转速,振动不应超过在最大连续转速下记录的最大振动值的150%。振动超过这个限值,但仍在表中的允许限值范围内,得到买方认可也可通过验收。
6.9.4.8 变速泵在超出其规定转速范围运行时,振动极限应不大于本文件的振动限值。
6.9.4.9 如果卖方可证明存在机械的和电学造成的跳动,只要其值不大于允许的峰-峰振幅的25%或6.5μm(0.25 mil),两者之间取较小值,可从工厂试验测量的振动值里以矢量的方式减去证实的跳动量。
==图35 转速大于3 600 r/min 或每级吸收功率大于300 kW(400 hp)的卧式泵振动极限==
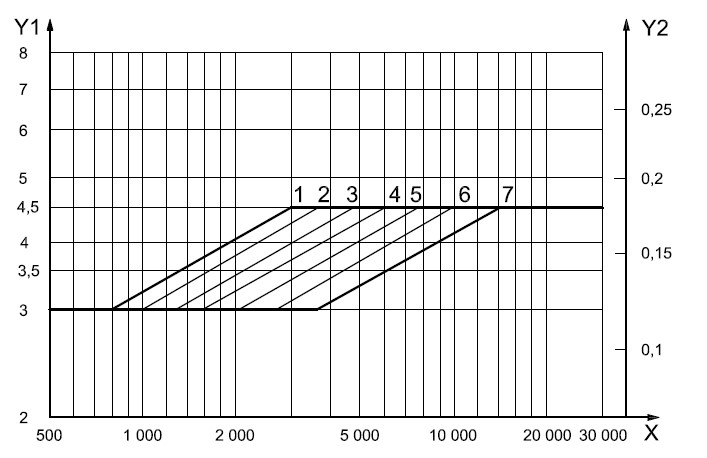
::: warning
X——转速,单位为转每分钟(r/min); 3——P=1 500 kW/级;
Y1——振动速度,单位为毫米每秒(mm/s); 4——P=1 000 kW/级;
Y2——振动速度,以in/s,RMS表示; 5——P=700 kW/级;
1——P≥3 000 kW/级; 6——P=500 kW/级;
2——P=2 000 kW/级; 7——P≤300 kW/级。
注1:3.0 mm/s~4.5 mm/s的公式是:vu =3.0(n /3 600)0.30[P/300]0.21。
注2:图35允许的离散频率的振动极限是:vf <0.67 vu。
:::