6.1.1 总体说明
6.1.1.1 所有的机械密封(无论何种型式或布置方式)都应采用没有台肩轴套的集装式设计。
API 610 标准要求泵的设计能够保证拆装密封时不干扰传动装置。如果泵是改装的泵,且不是可拉出式的结构,那么必须对比密封长度和泵到电机轴端之间的距离,以确保具有足够的轴向空间安装机械密封。
6.1.1.2 除非另有规定,A 型和B 型密封应采用旋转式补偿组件;如果指定,或者密封制造商建议且买方同意,A 型和B 型密封也可以采用静止式补偿组件。
::: warning
注:在本标准的范围内,旋转式补偿组件和静止式补偿组件在技术上被认为是等同看待的,但是,优先选择哪种补偿组件受到其他因素的影响。对于不同型式和布置方式的密封,优先选用旋转式补偿组件还是静止式补偿组件取决于普遍使用的数量和操作的可靠性。
:::
当选择旋转式或者静止式补偿组件时,宜考虑与设计,制造、安装和设备的维修相关的诸多因素。本章的其他条款和附录F.5 分别给出了旋转式和静止式补偿组件的相对优缺点和选择的影响因素。
6.1.1.3 除非另有规定,C 型密封应采用静止式补偿组件;如果指定或密封制造商建议且买方同意,C 型密封也可以采用旋转式补偿组件。
::: warning
注:见注6.1.1.2
:::
6.1.1.4 在安装或者拆卸的过程中,为了避免推、拉设备或调整转子时把径向或者轴向载荷传递到密封端面上,集装式密封应非常牢固的安装在一起(如设置定位板)。
6.1.1.5 如果密封端面平均直径处的线速度超过23m/s(4500 ft/min),应采用静止式补偿组件。
::: tip
注:当速度增加时,旋转补偿组件需要更快的变形反应,来使密封端面闭合。但是,在非常高的速度下(或者直径非常大),密封面的闭合力会变得非常大,以至于会影响密封的寿命。
:::
在下列情况下,宜考虑采用静止补偿组件:
- (1) 平衡直径超过115mm(4.5in)(见6.1.1.7);
- (2) 由于管路载荷、热变形或压力变形等原因使泵壳或者密封端盖变形或偏心;
- (3) 密封腔的安装端面与轴不垂直,高速旋转时不垂直度加重;
- (4) 密封端面的跳动量不能达到6.1.2.13 的要求(如单级泵、多级泵、ASME B73.1 和ASME B73.2 泵)。
6.1.1.6 本标准不包括机械密封零部件的设计,但零部件的材料和设计应达到指定工况要求。最大许用工作压力适用于所有的部件(参考泵壳耐压的定义)。
::: warning
注:在正常情况下,安装在密封腔中的密封元件不会经常在最大许用工作压力下运行。
:::
6.1.1.7 密封制造商应合理的设计密封端面和平衡系数使密封面产生的热量最小,并符合4.2 节中所期望的寿命及泄漏率的相关要求。平衡直径随密封设计结构的不同而不同。对于弹簧滑移式密封,平衡直径为与补偿密封环密封圈产生轴向滑动时相接触的那个直径。对于单端面的内侧密封,滑动表面随着内、外压力的变化而变化,如图10b)所示。对于金属焊接波纹管密封,平衡直径通常是波纹管的平均直径,它会随着压力而变化。在压力变化的工况下,应联系密封卖方来确定波纹管密封的平衡直径。
::: warning
注1:密封周围的环境温度会影响密封端面的生热和散热,从而影响密封性能。当讨论机械密封的平衡直径和密封的生热和散热时,请参考附录F2.1 和F2.2。
注2:对于泵的电机功率较小,或平衡直径和压力大于等于本标准中规定范围的机械密封,及布置方式3 密封,启动扭矩和密封功耗可能是一个比较重要的问题。
:::
6.1.1.8 所提供的密封应能够承受正常和瞬间的转子和静止部件之间的轴向相对位移。
注:对于高温多级泵来说,要特别考虑最大轴向相对位移。在启动时,泵和壳体之间会产生非常大的热膨胀差值。该差值可能超过了一些机械密封的承受能力。有些立式泵的轴向位置是根据电机的轴承确定的,在设计用于这种情况的密封时,应考虑轴向相对位移(例如,无轴承箱的管道泵和立式泵)。在某些情况下,工作压力也会使轴产生推力,此时,轴的轴向移动受到电机轴承的限制。
6.1.1.9 除非别有规定,O 形圈的安装表面(包括所有的孔和槽)应满足规定的粗糙度要求。对于安装静止O 形圈的表面,最大表面粗糙度(Ra)为1.6μm(63μin),对于安装滑动O 形圈的表面,最大表面粗糙度(Ra)为0.8μm(32μin)。
安装静止O 形密封圈的泵轴台阶上应具有最小半径为3mm(0.12in)的圆角,或最小1.5mm(0.06in)15°~30°的倒角。
为了防止装配时O 形圈的损坏及与认证试验的特殊要求相一致,集装式密封的倒角和圆角应足够大。
::: warning
注:集装式密封内部结构的倒角可以和本节规定值不同。
:::
6.1.1.10 O 形圈沟槽应根据全氟橡胶O 形圈设计尺寸
::: warning
注1:全氟橡胶的热膨胀性比其他大多数的O 形圈材料(例如氟橡胶)的热膨胀性更大。在为氟橡胶设计的O 形圈槽内安装全氟橡胶O 形圈会导致O 形圈损坏。从另一方面来说,在为全氟橡胶设计的O 形圈槽内安装氟橡胶O 形圈时是合适的。所以为了避免全氟橡胶O 形圈损坏,应采用宽槽作为标准O 形圈槽,同时也减少了所需的备件数量。
注2:全氟橡胶O 形圈的热膨胀损伤经常与O 形圈的化学膨胀损伤混淆,反之亦然。
:::
6.1.1.11 当密封腔压力低于大气压时,或对于布置方式3 的内侧密封,所有密封组件都应设计限位结构,以防止大气压力或者隔离压力导致密封元件移动(图10 给出了典型的限位设计结构)。当泵停止运转时,机械密封应在真空下还能保持密封性(参考6.1.2.14.1)。
==图10 布置方式3 密封和真空工况下内侧密封的限位装置==
==a) 结构限位== ==b) 压力限位(L 型非补偿密封环)==
::: tip
1-限位结构
Dbi>Dm>Dbo
:::
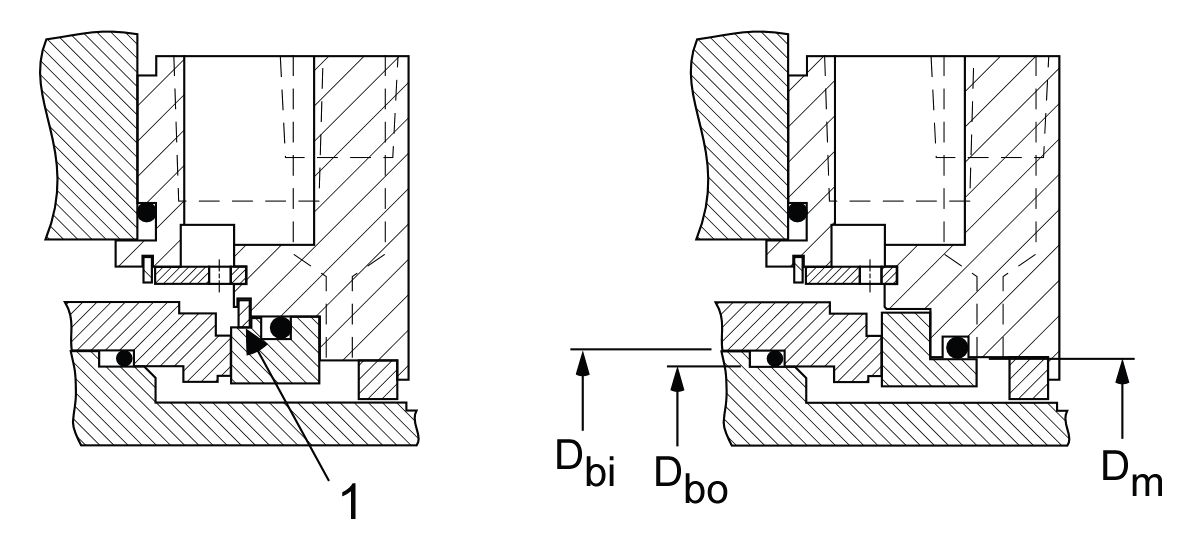
6.1.2 密封腔和密封端盖
6.1.2.1 密封端盖应由密封制造商提供。
6.1.2.2 除非另有规定,密封腔应由泵制造商提供。
==图11 密封腔类型==
==a) 传统型== ==b)外装型== ==c)内装型==
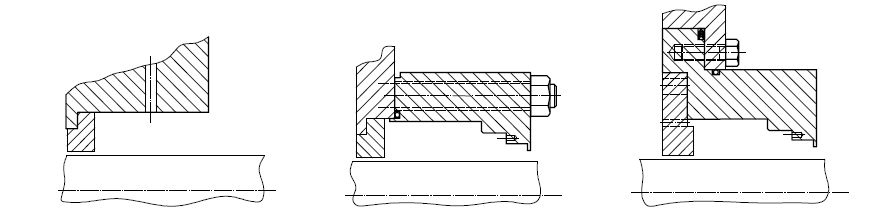
6.1.2.3 密封腔有三种类型:传统型、外装型、内装型。密封腔不需要满足安装填料密封的要求,图11为三种典型密封腔结构。
注:外装型密封腔类型灵活性大,非常适用于布置方式2和布置方式3密封。采用此种密封腔,可以优化轴向布置方式冲洗流体、隔离或缓冲流体的进出口位置,以便液流的流通。
6.1.2.4 泵制造商提供的默认密封腔是传统型密封腔[圆柱形腔体,与泵壳集成在一起,(图11a)]。
系列1 密封腔的尺寸应符合ASME B73.1 和ASME B73.2 所规定的腔体尺寸要求。
系列2 和系列3 密封腔的尺寸应符合API 610 所规定的密封腔尺寸要求。
符合本标准规定的密封腔设计要求有利于提高密封元件的可靠性和标准化。当密封腔与旋转件的径向间隙小于本标准的要求时,需要向用户阐明管路配置方案和结构要求。
密封的可靠性受到机械密封的旋转部件与密封腔内孔之间的径向间隙的影响。当密封操作工况比较恶劣时,如固体颗粒含量高或密封表面产生热量大,必须符合本标准所规定的最小直径间隙要求。改变一些化工行业中泵所采用的密封腔的传统设计结构,如采用带有流速调节器的大直径圆柱形密封腔或圆锥形密封腔,可以达到冲洗的要求或者提高密封性能。
系列1 密封适用于ASME B73.1、ASME B73.2 泵,系列2 和系列3 密封适用于API 610 泵。但是,也有可能把系列1 密封应用于API 610 泵,或在某些特殊的工况下,把系列2 和系列3 密封安装在ASME B73.1、ASME B73.2 泵上。当把不同密封系列的机械密封用在类型和工况不匹配的泵时,宜给予仔细考虑。
6.1.2.5 如果指定,内装型或外装型螺栓连接的密封腔应由密封制造商提供(如图11 所示)。
6.1.2.6 为了防止相对转动的部件之间相互接触,静止部件和旋转部件之间应具有足够大的直径间隙,其数值应符合本条和表1 的规定:
- a)为了加强密封端面附近流体的循环和冷却,对于接触式密封,密封的旋转部件与密封腔、密封端盖的静止内表面之间的最小直径间隙为6mm(1/4in)。
- b)对于具有非接触内侧密封的布置方式2 和布置方式3 的机械密封(2NC-CS 或3NC-XX),密封的旋转部件与密封腔、密封端盖的静止内表面之间的最小直径间隙为3mm(1/8in)。非接触密封产生的热量较少,仅有被密封介质粘性剪切产生的热量。
- c)机械密封金属部件的第一个径向接触点不应在补偿密封环或者非补偿密封环上(见注2)。
::: warning
注1:设置最小直径间隙的目的不应理解为当轴承失效或者其他机械和操作出现问题的工况下,密封元件可以用于限制轴的径向移动。
注2:6.1.2.6c 中的要求是为了在机械密封的旋转部件和静止部件之间的最小直径间隙超过表1 规定值的极少见的工况下,尽可地减少密封泄漏率和降低摩擦生成火花的可能性。在有毒有害、易燃的工况下,设计足够大的设计间隙对于提高密封的可靠性和人身安全是十分重要的。在下列工况下,应增加密封的直径间隙:
- (1) 轴承的磨损量超过了设计范围;
- (2) 泵的操作工况超过了许用操作范围;
- (3) 泵中控制轴和腔体径向位置的零部件可能会损坏,腐蚀或者磨损。
在危险工况下,确保泵的安装符合适当标准是十分重要的。在这些工况下,应定期进行操作条件监测、可控检维修。
注3:根据API 610 和ANSI B73 规定进行制造和维修的设备,这些最小间隙是适当的。但对于根据其他规定制造、安装、维修和操作的设备,这些间隙可能不够。在下面的情况,宜考虑采用更大的间隙:
- (1) 不符合API 610,API 682 中对轴、泵壳和密封的设计规定,不符合ANSI B73.1 和ANSI B73.2 中对轴和泵壳的设计规定的泵。
- (2) 泵安装时由连接管路系统所产生的安装应力和法兰应力超过API 610 ,ANSI B73.1 和ANSI B73.2规定的范围。
注4:这些最小间隙是用来防止旋转部件和静止部件之间接触,但是布置方式2 和布置方式3 的CW 型密封的内侧间隙还应充分满足隔离液或缓冲液的循环流量和密封端面的冷却要求。这对面对背的端面组合特别重要,其原因在于这种密封中的隔离液或缓冲液循环流动远离内侧密封。内侧密封的冷却不足,可能导致密封的可靠性降低。采用3CW-BB 和3CW-FF 的结构和采用泵送流体冷却密封腔的方法可以解决内侧
密封的冷却问题。
:::
==表1 密封旋转件和密封静止件之间的间隙==
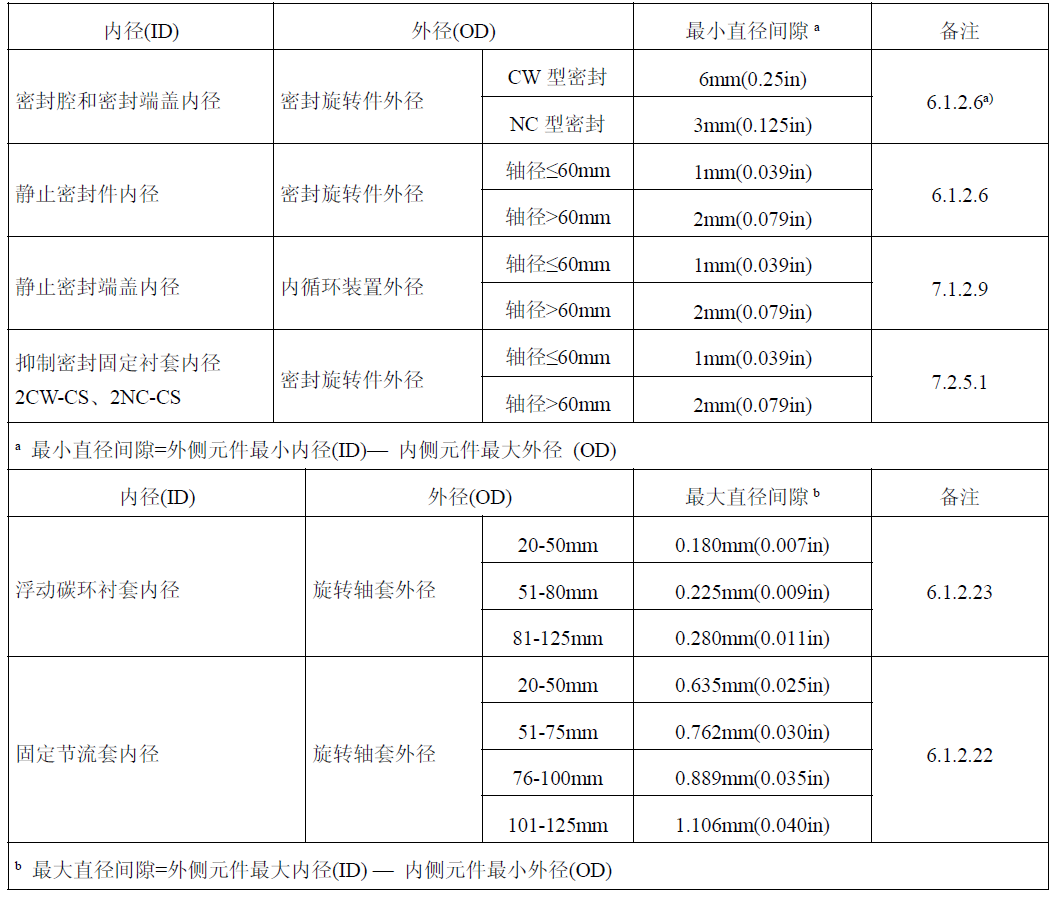
6.1.2.7 所有螺栓、螺母的应力应符合最大许用工作压力下的设计应力强度。密封腔应使用四个螺栓。螺栓的直径应符合6.1.2.4 中密封腔的尺寸要求。只有满足EN 13445 和ASME VIII 的应力要求,或者根据ASME16.20 要求需要采用较大压缩应力的缠绕垫片时,才能使用大直径螺栓。
6.1.2.8 密封腔的最大许用工作压力应当大于等于泵的最大许用工作压力(由泵制造商提供此数值)。密封腔应有3mm(1/8 英寸)的腐蚀裕量,同时具有较好的刚性,以避免产生变形(包括拧紧螺栓以压紧垫片时可能出现的变形),从而影响密封的工作性能。对于高合金材料,允许降低腐蚀裕量,但必须征得买方同意。此外,还需要满足以下要求:
- a) 除非有特殊说明,密封端盖必须加工好与螺栓相匹配的螺栓孔(不允许采用凹槽)。
- b) 应对密封端盖与密封腔的内径或者外径配合面提出同轴度要求,配合面必须与轴同心,总跳动量(TIR)不超过0.125mm(0.005 英寸),如图12 所示。其配合公差按照ISO 286-2 规定,为H7/f7。
- c) 密封端盖要有至少3mm(1/8in)厚的台肩,用来承受密封腔内压力施加到密封元件的轴向载荷,如图13所示。
==图12 密封腔同轴度要求==
==a) 外径配合==
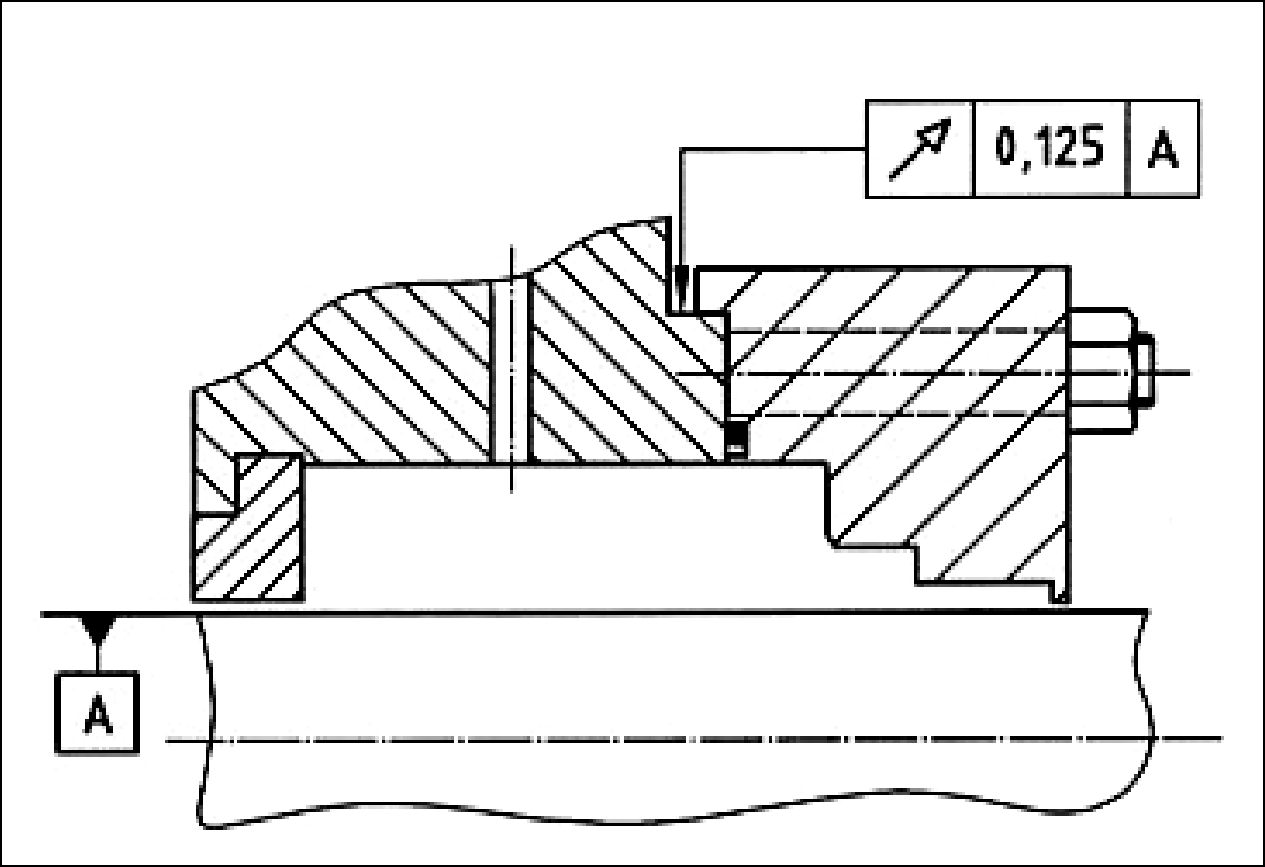
==b)内径配合==
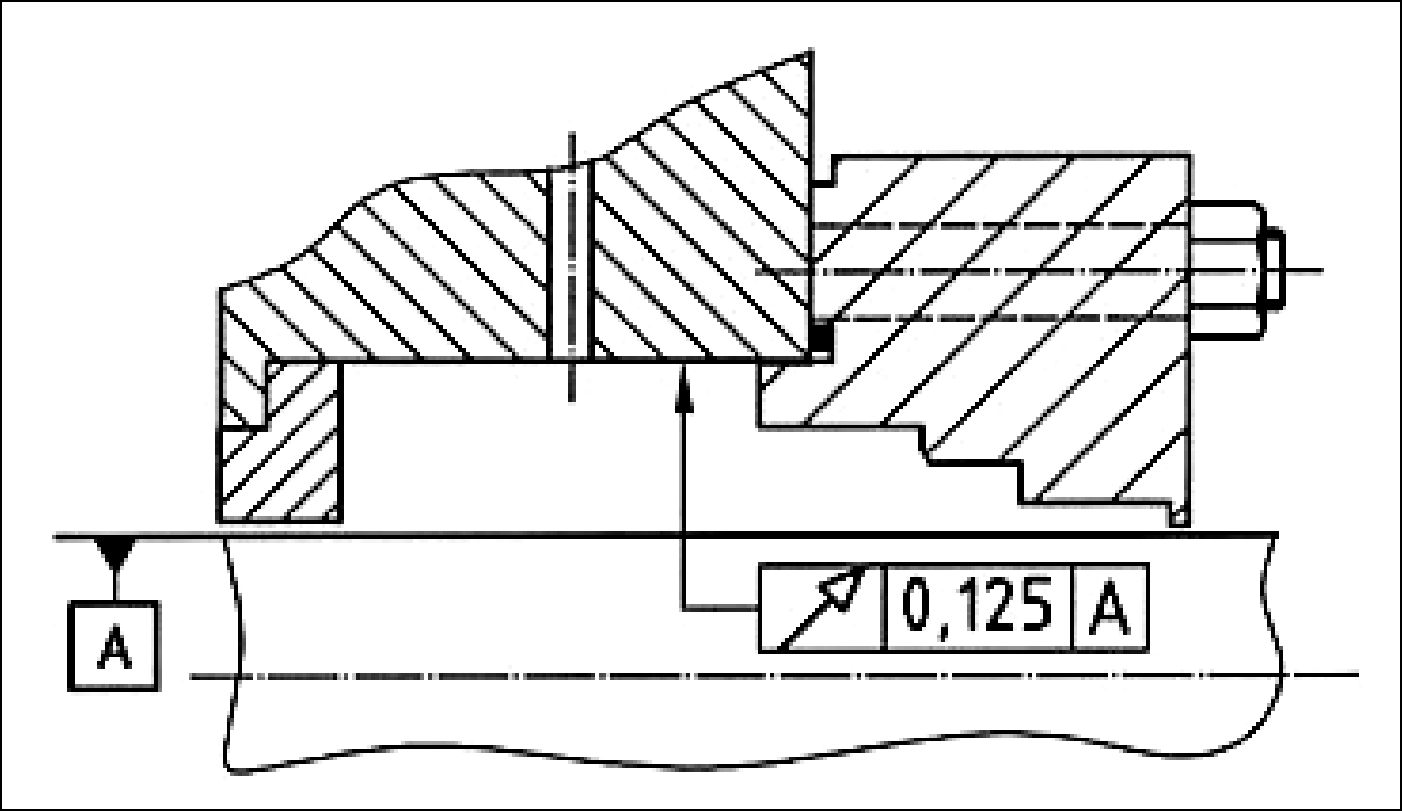
图==13 密封端盖台肩的局部视图==
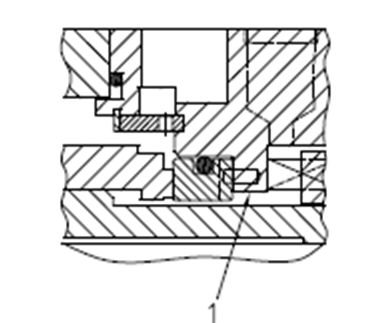
==图14 密封腔的端面跳动量==
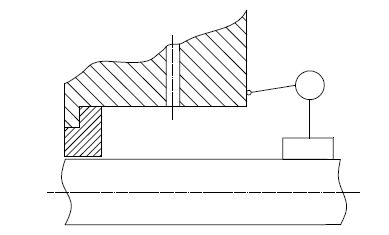
6.1.2.9 安装在泵壳上的任何零件材料的设计应力不能超过泵壳材料的设计应力。当泵的原始设计中没有提供泵壳材料的设计许用应力时,其值必须符合ISO 13709 的要求。
6.1.2.10 密封腔和密封端盖不需要提供诸如ASME Ⅷ等标准中要求的制造数据表、第三方检查报告及标志。
6.1.2.11 承压部件上应减少使用螺纹孔。为了防止泵壳体的承压部分发生泄漏,除了腐蚀裕量外,在光孔和内螺纹孔的周围和底部应保留有至少要等于螺栓名义直径的一半的金属厚度裕量。
6.1.2.12 承压件所用螺纹的具体要求应遵照ISO 261、ISO 262、ISO 724 和ISO 965 的规定、或ASME B1.1的规定。不得采用公制细牙螺纹和英制细牙螺纹。除非另有规定,泵腔体、密封腔、密封端盖之间连接优先使用API 610 表H.1 规定中的双头螺柱,而不采用带头螺栓。必须留出适当的空间以保证采用扳手或套筒来安装螺柱。所有紧固件制造商标志应至少6 毫米(1/4 英寸)或者更大(不包括垫圈和无头螺钉)。对于螺柱,标记应位于外露螺母上。
::: warning
注1:紧定螺钉是指一端具有内六角凹槽的无头螺钉。
注2:在小型泵上可能无法留出使用扳手或套筒安装密封端盖上螺栓的足够空间。
:::
6.1.2.13 密封制造商所设计的相对于密封腔内孔的密封腔端面跳动量(TIR)应小于等于0.5μm/mm(0.0005in/in),如图14 所示。
::: warning
注1:某些多台阶、细长轴的结构设计和一些ASME B73 中的泵可能满足不了本节的要求(参见6.1.1.5)。
注2:机械密封的性能会受到过大密封腔跳动量的严重影响。密封腔端面跳动量或密封腔配合面的跳动量可以表示泵轴同密封腔安装平面的垂直度。
:::
6.1.2.14布置方式1和布置方式2的接触式湿式密封(不包括抑制密封)的密封腔和辅助(支持)系统设计条件应设置在适当的密封操作工况下。低压差泵和处理高汽化压力流体的泵可能无法满足6.1.2.14.1和6.1.2.14.2规定的蒸汽压力裕量。假如密封腔条件不能满足规定的蒸汽压力裕量,密封制造商应做到如下要求:
- a) 根据指定的流体来确定密封和冲洗方案是否正确。
- b) 推荐密封腔的操作工况(最低压力和最高温度),能使密封达到安装后能正常连续运转三年,而不必更换的要求。
- c) 密封腔或密封端盖需安装两个冲洗接口,以便可以直接测量密封腔的压力。
- d) 除非空间限制,否则采用分布式冲洗结构。
::: warning
注:特殊规定参照F1.4
:::
6.1.2.14.1 在操作工况下,密封腔的压力至少要高于大气压力0.035MPa(0.35bar)(5psi)。尤其是泵的入口压力低于大气压时,该项要求更为重要。
6.1.2.14.2 在操作工况下,密封腔蒸汽压力裕量(VPM)(即密封腔压力减去流体的最大蒸汽压力)应满足6.1.2.14.2 a)的要求,如果达不到上述求,则应满足6.1.2.14.2 b)的要求。
- a) 不小于0.35MPa(3.5bar)(50Psi)。
- b) 密封腔中流体的绝对压力与泵送流体在泵送温度下的饱和蒸汽绝对压力的最小比值为1.3。
::: warning
注1:对于较高蒸汽压力的流体(如类似于乙烷之类的液化天然气,类似于乙烯之类的烯烃),推荐用户咨询密封制造商以确定密封的结构和适当的蒸汽压力裕量。
注2:关于蒸汽压力裕量(VPM),详见附录F1.4。
:::
6.1.2.15 如果配置节流套,应设计成可以更换的结构,且要保证它受到流体压力时而不会被推出。
6.1.2.16 如果用户指定或密封制造商推荐,可安装小间隙浮动节流套。节流套的材料和间隙应适应使用条件,并且需征得买方同意。
::: warning
注:配合适当的冲洗方案,小间隙节流套可以达到以下目的:
- a) 升高或者降低密封腔压力;
- b) 隔离密封腔流体;
- c) 控制进出密封腔的流体流量。
:::
关于节流套应用的其他指导可参考F.5.3。
6.1.2.17 对于机械密封数据表指定的密封端盖和密封腔上的连接接口,应在零件上做出永久性标记(如压印或浇铸)。应根据表2 确定标记的符号、尺寸和位置(也可以参看图15 确定泵送介质侧接口和大气侧接口的轴向位置)。条件允许时,采用字母“I”和“O”(进口和出口)在接口处做出标记。对于卧式泵,0°定义为顶部的竖直方向。对于立式泵,冲洗接口(用字母“F”表示)位置为0°(详见图2~图6)。当泵或密封端盖的尺寸不允许在密封端盖上设置所需要的连接接口时,密封卖方应建议泵卖方在泵壳或密封腔上设置所需的连接接口。如果采用切向连接接口,密封腔中的钻孔应遵照表2 的要求。但是,密封端盖上的内螺纹接口可以不同于表2 的要求。当密封腔上没有足够的空间加工内螺纹接口时,就需要泵制造商和密封卖方共同研究以给出解决方案(参考附录E)。
采用不同尺寸的接口,可以减小不正确装配的可能性,特别是在维修情况下。用户应注意到表1 中所指定的连接尺寸和位置并不适用于小型泵。
==表2 密封腔和密封端盖上接口的规格和标识==
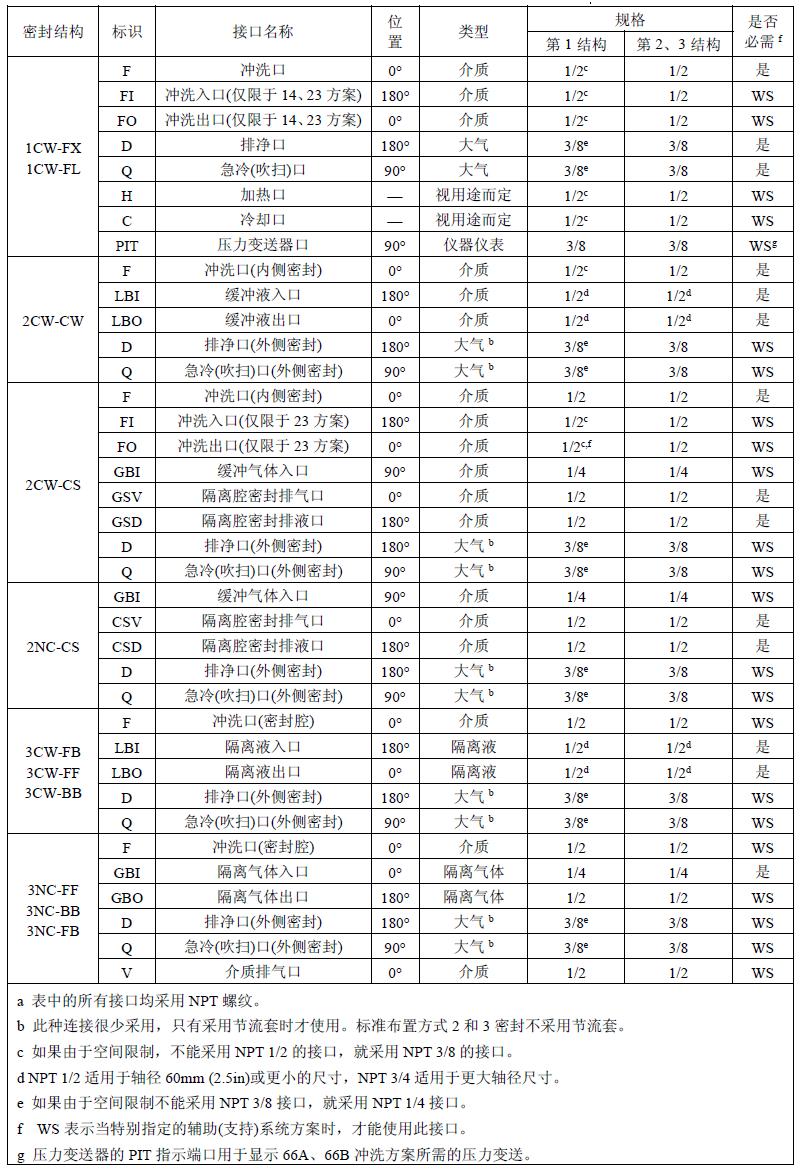
==图15 机械密封的接口==
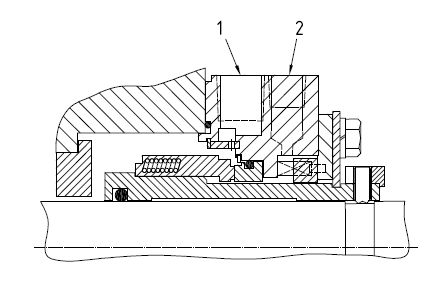
::: tip
1 泵送介质侧;
2 大气侧
:::
==图16 红色塑料塞和警示标志示例==
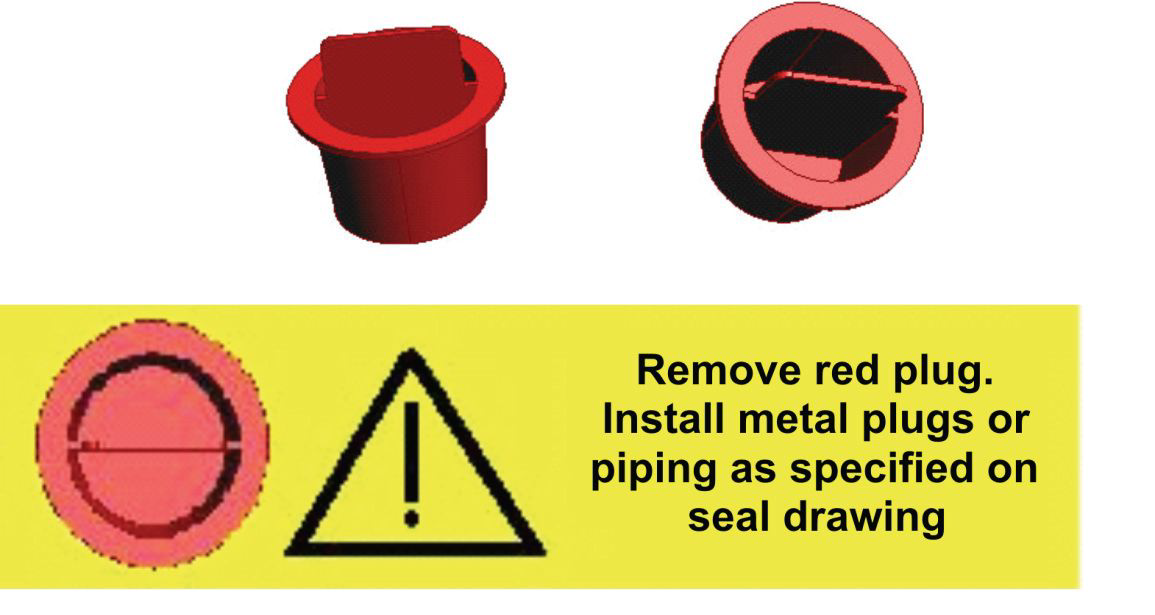
6.1.2.18 接口和螺塞
6.1.2.18.1 运输时,密封端盖的螺纹接口应塞入塑料塞。这些螺塞国际上通用为红色,中心有把手,能够很容易地从螺纹接口拔出,并与金属螺塞有明显区别(见图16)。应在塑料塞或者密封上贴上国际通用的黄色警示标志,标明应在操作之前移除这些塑料塞。警示标志应包含国际警示标志和使用英语、法语、西班牙语、德语、日语和中文的以下文字:“去除红色塑料塞,按照密封图纸规定安装金属螺塞或者连接管路”,如图16 所示。不得对塑料塞、警示标志和密封端盖喷漆。运输时,除了密封端盖上的螺纹接口以外,其他螺纹接口都应安装金属螺塞。
6.1.2.18.2 应配备足够用来堵住密封端盖上所有螺纹接口的金属螺塞。金属螺塞的材料应与端盖的材料相同,或者在特殊工况下,螺塞的材料具有更好的抗腐蚀的性能。螺塞应采用塑料袋单独包装,塑料袋上应带有标记为“所有未使用的密封接口应安装金属螺塞”的警示标志。在密封图纸和说明书上应具有同样的警示标志。除了包装机械密封的包装箱中包含一份密封图纸外,在包装金属螺塞的塑料袋中也要包含一份密封图纸。螺塞应该使用实心圆柱或实心六角头螺栓制造,并符合ASME B16.11 的尺寸要求。由于方头螺塞在安装和拆除时容易损坏,金属螺塞不允许采用方头螺塞。
::: warning
注:ASME B16.11 禁止采用中空螺塞或型芯螺塞;在工业中,这些螺塞曾多次发生失效事故。
:::
6.1.2.18.3 安装螺塞时应遵循工厂实践经验,在螺纹上使用润滑剂或密封剂,以确保螺纹的密封性。在密封端盖螺纹连接处使用PTFE 胶带、防自锁剂或抗磨剂可能会导致密封污染,宜谨慎使用。
6.1.2.19 所有的连接管路都要符合其连接的密封腔或密封端盖的水压试验压力等级。
6.1.2.20 接触式湿式密封的密封端盖和密封腔(包括隔离或缓冲腔)应该能够在启动和操作过程通过管道系统自动排气。除了冲洗方案23 以外,只有在密封买方同意的情况下,才能把排气系统设计成手动操作,同时还应该满足如下要求:
- a) 对于小型卧式泵,排气接口的高度不足以达到冲洗方案11 连续操作的要求,如果买方同意,排气接口可以位于止回阀的上游。
- b) 如果接触式湿密封应用于立式泵中,密封腔或密封端盖的排气接口尺寸不应小于3mm(1/8 in),以便排除流体中夹带的气体,且此接口应位于密封腔的最高处(如图17)。应用于立式泵的布置方式2(2CW-CW)和布置方式3 密封中的接触式湿密封的外侧密封也具有相同的要求。
- c) 对于采用冲洗方案23 的卧式泵或立式泵,或采用冲洗方案11,21,31 和41 的立式泵,要在其管路系统内安装单独的排气接口。采用冲洗方案2 的立式泵应在密封端盖上设一个排气接口。除此之外,如果在密封腔上设计其他手动排气装置,需要经过买方的同意。
- d) 由于泵内压差而引起正向流动的小型密封冲洗系统中,可能不需要手动排气(即小型泵上管路较短的冲洗方案11 或13)。因为泵一旦启动就会迅速地从管路或密封腔中带走所有的气体。
- e) 布置方式3 的非接触密封在启动前,要排净密封腔中的气体,且在泵操作时要避免气体聚集在泵内。
::: warning
注:可以在卧式泵轴的浮动衬套上最顶部的死角开孔,以便泵内密封腔能够自然排气。当采用管线进行排气无法实现时,也可以采用这种排气方法。
:::
6.1.2.21 要根据具体情况钻孔,最小孔直径为5mm(3/16 in)。
6.1.2.22 喉口衬套的最大直径间隙不能超过表1 中的规定值。
==图17 立式泵的密封腔和密封端盖==
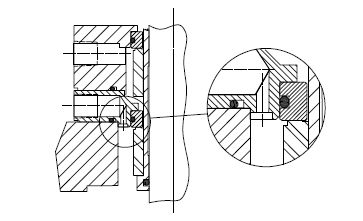
6.1.2.23 浮动石墨节流衬圈的直径间隙如表1 所示。
注:如果将衬套设计成在泵送温度下具有最大直径间隙,当操作温度低于此温度时,则衬套的径向间隙就会大于表1 中给出的数值。若用户想在一定的操作工况范围内减小衬套的间隙以减小泄漏,可以咨询密封制造商关于材料选择的建议或者采用周向分瓣浮动石墨节流套,该结构可以在一定温度变化范围内,维持给定的间隙。
6.1.2.24 如果指定,密封腔可以安装加热夹套或加热元件。买方、卖方和制造商之间应对加热要求达成共识。
注:密封夹套可以同时作为加热和冷却的温控元件,但不推荐夹套用于冷却目的,因为该方法的效率较低,并且可能产生污垢并引起堵塞。蒸汽可有效的用于高温泵的冷却,并且能够在泵转速较低的工况下,防止流体的凝固。当使用密封夹套时,若对密封腔内孔进行了机加工,应该注意保证其最小壁厚要求。
6.1.2.25 所提供的连接接口需要满足5.1 条的要求。由于空间限制,密封端盖不能设置接口时,如果买方同意,可以由泵制造商提供所需的连接接口。
6.1.2.26 密封端盖、密封腔、抑制密封腔和泵壳的所有连接面都应该采用约束型的密封件,以防止泄漏,如图18 所示。密封端盖和密封腔的金属接触面应该能够控制密封件(O 形圈和金属缠绕垫片)的压缩量。连接面的设计应该防止垫片被挤压到密封腔内部,以避免干扰密封的冷却。但是由于空间的限制,可能达不到这个要求,应该将其他的密封端盖设计方案提交给买方,并征得其同意。
==图18 连接面密封方式==
==a) O 形圈== ==b) 螺旋缠绕垫片==
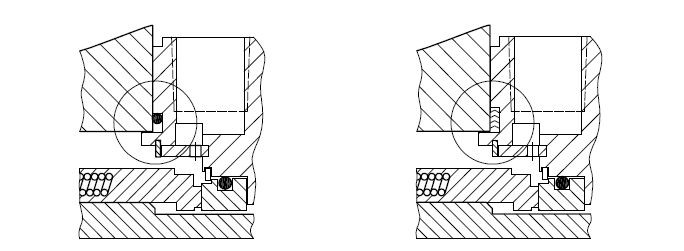
::: warning
注:为了减少跳动,需要依靠金属和金属之间的接触面来保持旋转补偿组件的密封端面和轴线相垂直。
:::
6.1.3 集装式密封轴套
6.1.3.1 密封轴套应由密封制造商提供(关于辅助轴套详见6.1.3.10)。轴套应在一端与泵轴密封。密封轴套应伸出密封端盖的外表面。
::: tip
注:轴和轴套之间的泄漏不能与机械密封的泄漏相混淆。
:::
6.1.3.2 泵制造商需向密封制造商提供泵轴的直径和公差,并保证轴与轴套的径向配合为ISO 286-2 的F7/h6。根据本国际标准所包括的密封尺寸范围,F7/h6 配合间隙是0.020mm(0.0008in)到0.093mm(0.0037in),随轴径不同而变化。采用F7/h6 配合间隙的目的是减小轴套跳动(如图18)并方便安装、拆卸。采用缩紧盘时需要更小的配合间隙,且需满足收缩圆盘制造商的设计标准(见图19)。
API 610 要求轴径公差为h6,但在特殊情况下泵轴轴径的公差可以不是h6。在这种情况下,密封制造商应该确保合适的配合。
::: tip
注:也可选用能达到这个同轴度要求的其他连接方法,这需要密封买方与泵制造商和密封制造商协商。
:::
==图19 密封轴套跳动量==
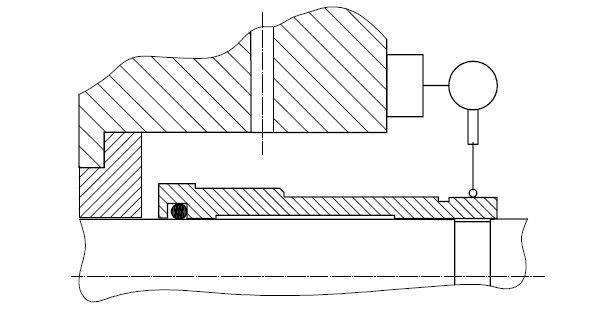
6.1.3.3 应提供为旋转元件在轴套上定位的结构。
注:该规定的目的是帮助密封件的组装,使机械密封的补偿组件定位在适当的轴向位置,以获得正确的弹簧载荷。用于确定关键点的轴肩、孔的结构都是与此相同的目的。采用这些结构可以减少由于测量不精确或者类似误差引起的装配错误。
6.1.3.4 除非另有规定,轴与轴套间的密封应该采用橡胶O 形圈或柔性石墨环。金属密封件通常不可靠,它会损坏轴,并且拆卸困难。轴和轴套间的密封件的材料宜比轴材料软。
6.1.3.5 轴与轴套间的O 形圈密封应该安装在靠近叶轮的一端。当O 形圈需要穿过轴上的螺纹进行安装时,轴上螺纹外径与O 形圈内径的直径间隙最小为1.6mm(1/16in),变直径的过渡段处需要设计倒圆或倒角(参见6.1.1.9)以避免损坏O 形圈。
::: warning
注:这样确定O 形圈的位置是为了防止轴套中积累泵送介质,避免拆卸困难。
:::
6.1.3.6 当轴与轴套的密封位于轴套外侧时,应能保证轴与轴套间密封的可靠性。
::: warning
注:柔性石墨环通常用于金属波纹管密封中,位于轴套外侧。
:::
6.1.3.7 在轴套最薄截面处,轴套的最小径向厚度为2.5mm(0.10in)。当利用伸出密封端盖的轴套来安装定位板,并需要在轴套上开设沟槽时,此时不适用轴套最小厚度的要求。
安装紧定螺钉位置的轴套厚度需要符合表3 的要求。在满足这些壁厚要求的轴套外表面开设用于安装紧定螺钉的凹孔时,其深度应该不超过0.50mm(0.020in)。
::: warning
注1:安装紧定螺钉附近的轴套厚度,要能防止由于拧紧紧定螺钉而产生的轴套变形。
注2:过薄的轴套容易变形。
:::
==表3 安装紧定螺钉的最小轴套厚度==

6.1.3.8 轴套应沿着它的整个长度方向全部机加工和精加工,以保证轴套的内孔和外径是同心的,且同心度跳动量(TIR)不超过25μm(0.001in)。
6.1.3.9 沿着长度方向,轴套孔内径要与轴保持一定的间隙,只在轴套的两端或两端的附近与轴保持定位配合。
::: warning
注:这样做可以在达到所需配合精度的情况下,更方便安装和拆卸。
:::
==图20 辅助轴套布置方式==
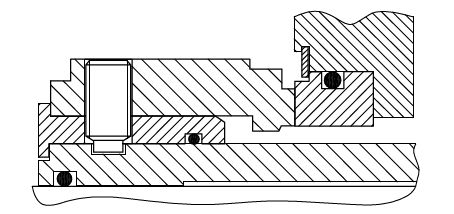
6.1.3.10 密封轴套应该尽可能地设计成为一个整体的结构。对于布置方式2 和布置方式3 的集装式密封,为了方便密封元件的组装,也可以设置一个辅助轴套。应该根据6.1.3.3 节规定的定位方法,将辅助轴套轴向定位在密封轴套上。辅助轴套应该和轴套同心安装,不得超出轴套,如图20 所示。
6.1.3.11 传动环的紧定螺钉不能通过带有间隙的非配合表面,轴套内腔的间隙除外。对于简支泵,在这个区域轴会加工凹形台阶。为了防止密封安装过程中损坏O 形圈,凹形台阶区域宜适当倒角。
注:如果将紧定螺钉拧紧在轴上,那么在轴表面形成的凹坑会把它附近的金属推起而对轴造成损伤。如果这个损伤区域在轴套内部,那么在轴套移开前是不能被修复的。对于双支点泵,在拆卸轴套时,轴套的全部长度都要通过损坏区域。这就使得轴套与轴产生磨损或者损坏轴和轴套。这个问题对于悬臂泵来说还不是很严重,因为在拆卸轴套时,只有一小部分轴套长度要通过损伤区域。
6.1.3.12 传动环的紧定螺钉要有足够的硬度,才能确保其嵌入到泵轴中。泵和密封制造商应该保证泵轴和传动环的紧定螺钉之间有足够的相对硬度差值,参考附录F.3。
6.1.3.13 密封制造商应该保证传动环的紧定螺钉具有足够的数量和尺寸来满足工况条件下实现旋转传动和轴向定位。传动环和紧定螺钉的结构应能够保证在由150%的最大额定压力(4.1.2 条规定)所产生的轴向载荷下轴套保持轴向定位。轴向载荷是由泵轴和密封平衡直径确定的环形面积与压力的乘积得到,计算详见F.3。
6.1.3.14 为了传动轴套或轴向定位,当使用九个以上的紧定螺钉时,需要征得买方的同意。不推荐在悬臂泵的轴上加工浅坑的方法来定位紧定螺钉。因为这会增加轴上应力,减少轴的疲劳寿命。只有在轴套的轴向位置确定后,才能在轴上加工浅坑。应确保所钻浅坑与传动环上的紧定螺钉孔对准,以便当拧紧紧定螺钉时,传动环与轴套不产生扭曲变形。
::: warning
注1:当轴的尺寸和密封压力增大时,轴套的轴向力(压力乘以面积)也要增大。当紧定螺钉数量增加时,传动环强度削弱,且每个螺钉所承受的力减少。
注2:当在泵轴上加工与紧定螺钉配套的浅坑时,除非采用倒角或其它的去除多余金属的方法,否则会在浅孔的附近有突出的钻唇。该突出的钻唇会损坏柔性石墨密封圈或橡胶O 形圈。
注3:当更换集装密封时,不允许使用轴上已经存在的浅孔。
注4:轴肩处能够为密封件提供轴向定位,在安装过程中降低轴上密封件损坏的可能性。
:::
6.1.3.15 如果密封或泵的制造商指定或推荐,并得到买方的许可,可以采用除了紧定螺钉以外的装置以进行轴向定位和传动轴套。例如胀接联接套(如图21 所示)和安装在轴上凹槽内的分瓣紧固环(如图22)。
::: tip
注:这些设计造价较高,一般仅用于无备用泵的情况下。采用这些结构可以用于轴套所受轴向力非常大的情况,避免由于锁紧紧定螺钉而损坏轴。
:::
==图 21 胀接联接套==
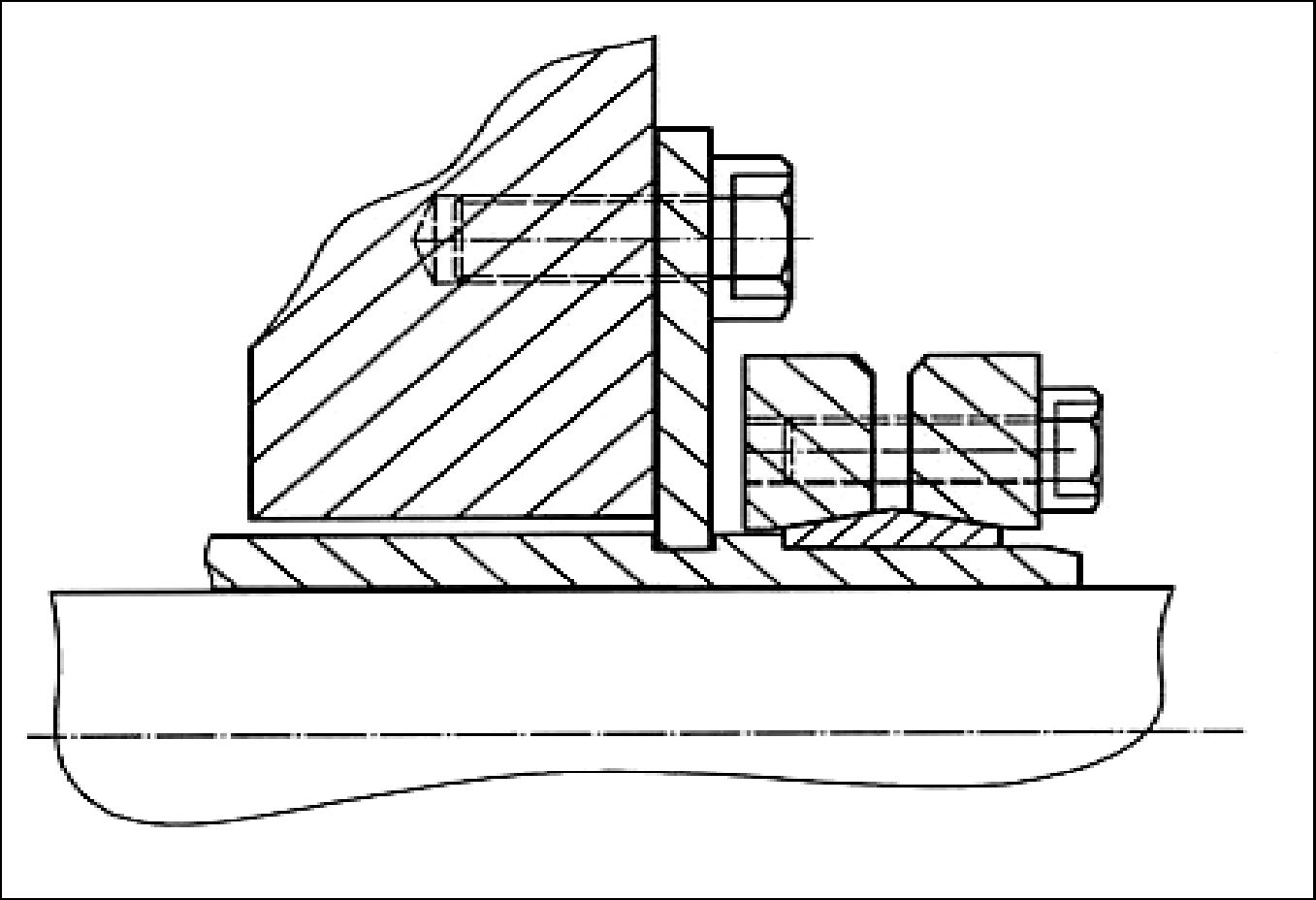
==图 22 分瓣紧固环密封轴套==
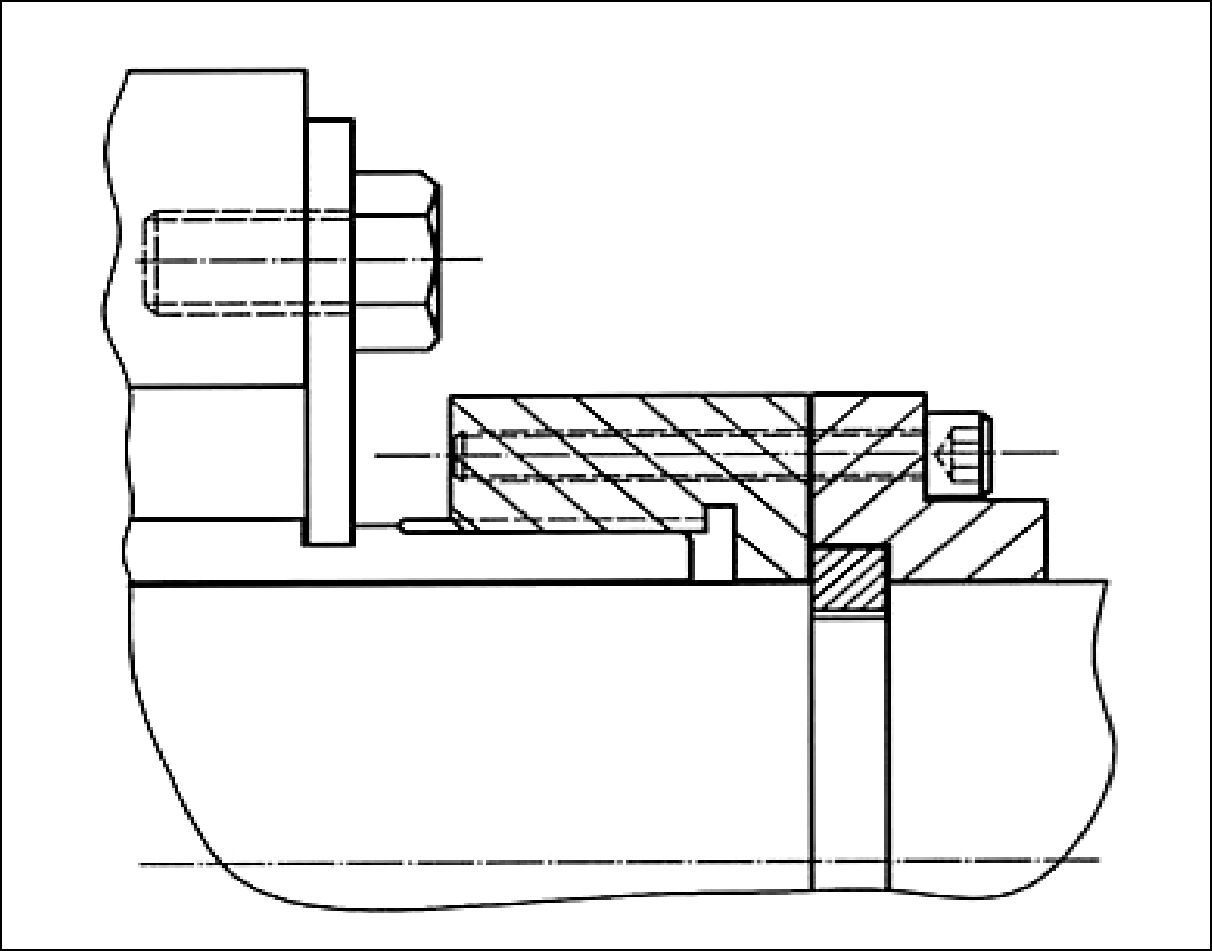
==图23 夹持密封环方式==
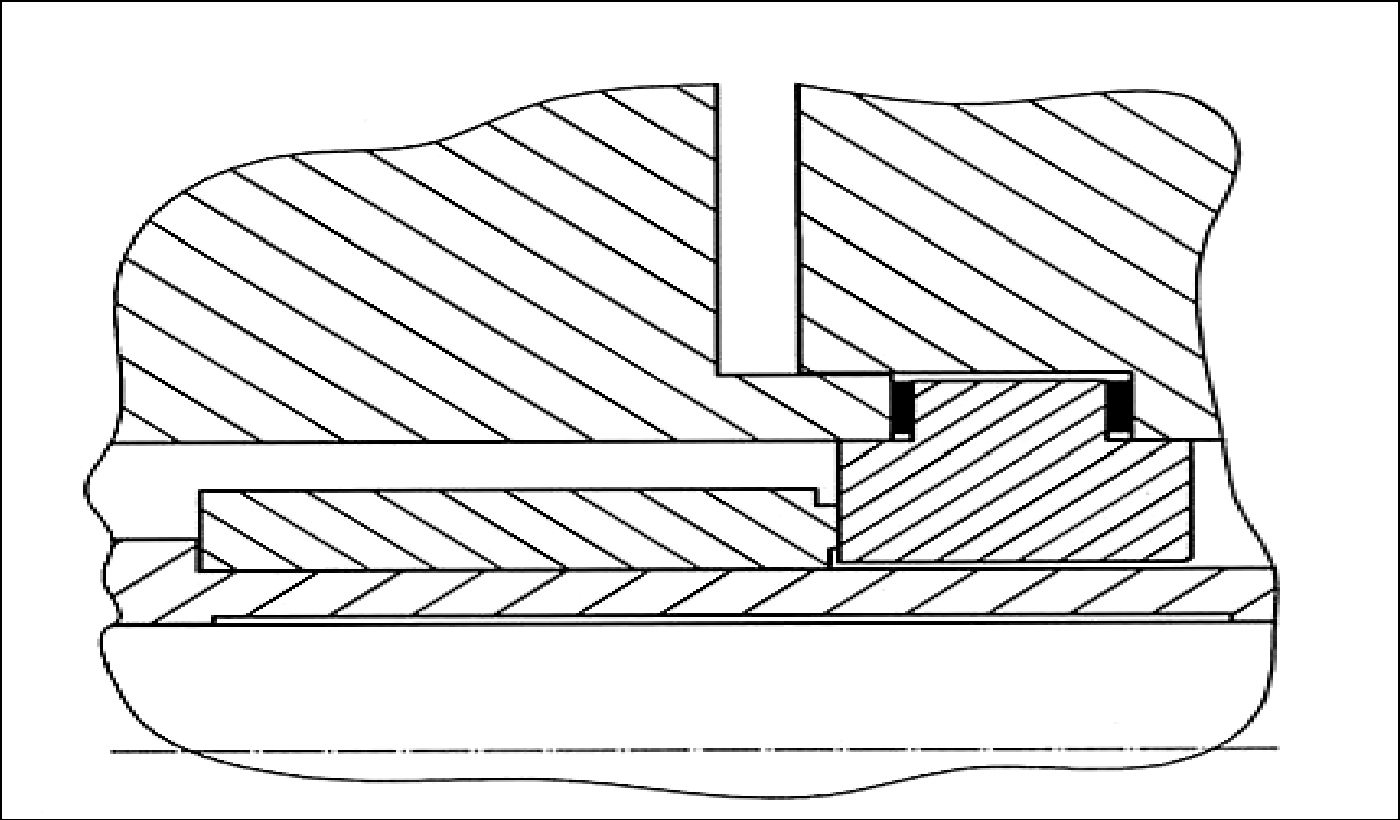
6.1.4 非补偿密封环
6.1.4.1 非补偿密封环的防转机构的设计结构应考虑到尽量减小密封面的变形。除非买方同意,否则不应采用夹持密封环方式的方法来防止非补偿密封环转动,如图23 所示。
注:密封面平面度是保证密封达到低泄漏和良好密封性能的关键,夹持密封环的防转设计方法很容易使密封环变形。
6.1.4.2 非补偿密封环的布置方式及其在密封端盖上的安装方式,应便于密封环的冷却,并避免热变形。
::: warning
注:安装在密封端盖上的非补偿密封环最内侧,与过程流体接触很少,因而不能有效地散热。可能会由于温度梯度而导致端面变形。
:::
6.1.5 补偿组件
6.1.5.1 如果买方指定且卖方同意,A 型密封也可采用单弹簧
::: tip
注1:多弹簧密封比单弹簧密封轴向上尺寸更紧凑一些。当采用双端面密封时,多弹簧更加适用。多弹簧结构也提供了更加均匀的压紧载荷。
注2:应用单弹簧密封时,一般需要增加6mm(0.25in)~13mm(0.5in)的轴向空间。对于单端面密封,单弹簧有利也有弊。单弹簧可以采用较低的弹簧刚度达到相同的端面载荷,这使得它更能够承受轴向偏心(密封轴向定位误差),这个优点由于集装式密封的使用而被掩盖了。
注3:对一些腐蚀性的流体密封,单弹簧的横截面比较大,所以能够提供更多的腐蚀裕量。多弹簧更适合放置在泵送流体之外,这样就能够避免弹簧置于腐蚀介质中。
:::
6.1.5.2 补偿组件不能依赖静态搭接进行密封因为搭接方式不能使补偿组件产生滑动配合,意味着禁止设计搭接旋转式补偿密封环。补偿密封环可
以采用过盈配合或垫片密封结构。
6.1.6 材料
6.1.6.1 概论
6.1.6.1.1 除非密封数据表另有规定,密封元件所用材料应满足6.1.6.2~6.1.6.9。
::: warning
注1:正确地选择材料是机械密封可靠运转的关键。选择材料取决于密封接触流体的性质,如一些关键参数、操作温度、压力、速度、润滑性能及化学相容性。当买方对操作工况下材料的相容性有疑问时,宜征求封制造商意见。关于材料的适当选择,参见NACE(美国防腐工程师协会)腐蚀工程师的相关参考用书。
注2:材料的选择可以根据密封元件的功用以及与其接触的流体特性变化而变化。当双端面密封应用于腐蚀介质工况时,没有接触腐蚀流体的密封元件与接触腐蚀流体的密封元件采用不同材料是很常见的。
:::
6.1.6.1.2 如果密封制造商为指定的工况推荐更好的或其它备选的材料,应在订单(报价单)中列出。
6.1.6.1.3 当指定采用本标准材料以外的其他材料,或用于工程密封的材料,都要标出其标准牌号(如ISO,EN,ASTM 等)和材料等级。如果没有这些资料,制造商应该根据要求提供材料规格,物理性能、化学性能和试验要求。
6.1.6.2 密封端面
6.1.6.2.1 每套密封装置都包括一个补偿密封环和一个非补偿密封环。
::: warning
注1:本标准不适用于密封环为分半结构的剖分式机械密封。
注2:以下是一般准则。密封端面材料众多,每一种都具有相对的优点和缺点。应咨询密封制造商以选择满足特定工况下的最好密封端面材料组对。事实上,在没有特定说明的情况下,不应将任何端面材料或者端面材料组对排除在外。但是为了符合本标准规定,端面材料或端面材料组对必须通过相关认证试验。
:::
6.1.6.2.2 除了6.1.6.2.4 规定的要求,密封端面组对中的一个密封环必须采用经过浸渍处理的高级防起泡石墨环,以减少磨损、防止化学腐蚀、减小孔隙。
6.1.6.2.3 对于系列2 和系列3 密封,根据化学相容性和密封制造商的推荐,其密封端面组对中的一个密封环应该采用反应烧结碳化硅(RBSiC)或无压烧结碳化硅(SSSiC)。这些材料都有多个级别,因此,制造商应该说明每套密封所用碳化硅的类型和级别。
::: warning
注:附录B2.3 提供了制造和使用反应烧结碳化硅RBSiC 和无压烧结碳化硅SSSiC 的说明。
:::
6.1.6.2.4 介质含有颗粒,黏度较高和高压工况时,机械密封可能需要硬对硬的密封端面材料组对。除非另有规定,补偿密封环和非补偿密封环材料都应是碳化硅。由SSSiC、RBSiC、加碳SSSiC、加碳RBSiC和碳化钨的硬对硬密封端面材料组对应用也很广泛,但需要征得买方的同意。
::: warning
注:关于如何选择最优的硬对硬密封端面材料参看附录B.2.4。
:::
6.1.6.2.5 补偿密封环和非补偿密封环应是同质材料,除了碳化硅和碳化钨那样的耐磨材料外,可以通过采用硬化涂层的方法提高材料的耐磨性,但硬化涂层不能作为唯一的抗磨措施。
::: warning
注:有关密封面材料的温度限制可参阅附录B.2。
:::
6.1.6.2.6 密封制造商应说明所指定的密封端面材料组对能否适用于泵制造商用水进行的性能试验。如果不适用,则密封制造商应推荐其他密封端面材料用于泵制造商用水进行性能试验。
6.1.6.3 轴套
除非另有规定,密封轴套应该是不锈钢轴套(316、316L 或316Ti,或者同等材料,参见附录B.1)。用于腐蚀工况下合金泵的密封轴套应该使用与泵壳相同的合金材料,或者具有更好抗腐蚀能力的材料。
6.1.6.4 弹簧
除非另有规定,多弹簧密封的弹簧应使用C-276 合金或C4 合金材料。单弹簧密封的弹簧应该使用316不锈钢材料。
注:在选择弹簧材料时应考虑弹簧横截面积。横截面积大的弹簧,如单弹簧,不易被腐蚀,而多弹簧的横截面积较小,所以相对容易被腐蚀。例如, C-276 合金适用于多弹簧密封,而在相同工况下316 不锈钢弹簧只适用于单弹簧密封。
6.1.6.5 辅助密封
6.1.6.5.1 除非另有规定,否则O 形圈应采用氟橡胶(FKM)。附录B.3 给出了氟橡胶的温度范围。
6.1.6.5.2 除非另有规定,如果氟橡胶(FKM)受到工作温度和化学相容性的限制而不能使用,则O 形圈应使用全氟化橡胶(FFKM),详见附录B.3。
6.1.6.5.3 密封制造商使用的辅助密封的供应商应该在炼油、化工、管道运输行业中,具有相同工况下工作至少一年以上的两个成功安装案例。密封制造商应该基于以前应用于炼油、化工、管道运输行业中的成功经验优先选择辅助密封的材料类型和等级。关于辅助密封的认证试验应包含销售商/材料等级/型式/硬度等信息。附录I 规定:其它销售商提供的同等公称硬度(HSA±5)、相似等级、相似类型的辅助密封,可用成形产品取代而无需附加认证试验,详见附录I。
6.1.6.5.4 除非另有规定,如果橡胶不能满足使用温度和化学性能的要求,应选择柔性石墨作为辅助密封材料。
6.1.6.6 金属波纹管
除非另有规定,否则B 型密封的金属波纹管材料应使用C-276 合金,C 型密封的金属波纹管材料应使用718 合金。如果密封制造商推荐,且买方同意, 718 合金也可以用在B 型密封上。
6.1.6.7 密封端盖
6.1.6.7.1 除非另有规定,否则密封端盖应使用不锈钢(316、316L 或316Ti,或者同等材料,参见附录B.1)。用于腐蚀介质的合金泵的密封端盖材料应与密封腔材料相同,或者采用耐腐蚀性能和机械性能更好的材料。
6.1.6.7.2 除非另有规定,否则应按6.1.6.5.1 和6.1.6.5.2 要求,当工作温度低于175℃(350℉)时,密封端盖与密封腔之间的密封结构应采用O 形圈。当温度超过175℃(350℉)度或另有指定时,应该使用柔性石墨+304 或316 不锈钢缠绕垫片。
::: warning
注:采用缠绕垫片时,需要相对应的垫片全压缩状态的螺栓拧紧力矩。关于缠绕垫片的螺栓拧紧力矩要求参见6.1.2.7。
:::
6.1.6.7.3 如果需要安装铭牌和旋向箭头标识,则其材料应为奥氏体不锈钢或镍铜合金(UNS N04400)。铭牌和旋向箭头的固定销也应是相同的材料,不允许焊接。旋向箭头应用钢印打在双支点泵传动端/非传动端密封端盖顶部。
6.1.6.8 螺栓连接的密封腔
6.1.6.8.1 采用螺栓连接的合金泵的密封腔材料应与泵壳材料相同,或者采用防腐性能和机械性能更好的材料。除非另有说明,泵的密封腔材料应使用不锈钢(316、316L 或316Ti,或者同等材料,参见附录B.1)。
如果螺栓连接的密封腔在高温环境中工作,且密封腔材料与泵及连接螺栓材料不同时,买方应考虑材料的热膨胀性能,以避免产生应力及与垫片相关的问题。
6.1.6.8.2 密封腔与泵壳之间的垫片材料应遵照6.1.6.7.2 的要求。
6.1.6.9 其他零部件
6.1.6.9.1 除非另有规定,弹簧座、传动销、防转销和集装密封内部的紧定螺钉都应具有或优于AISI 316不锈钢(详见附录B.1)所具有的硬度和防腐蚀性,或者是更好的材料性能。
6.1.6.9.2 泵卖方和密封卖方应确保外部传动元件对工作环境具有相应的防腐性能(详情请参阅附录E)。紧定螺钉应有足够的硬度和承受载荷,或者使用其它方法(比如定心钻孔、分瓣环或缩紧盘),参见6.1.3.12和6.1.3.13。
如果硬化碳钢紧定螺钉不适用于工作环境,需采用硬化不锈钢紧定螺钉(如沉淀硬化不锈钢)。
6.1.6.10 焊接
6.1.6.10.1 管件、承压件、旋转件和其他承受高压零部件的焊接,焊接修补以及和任何不同金属材料之间的焊接应由符合相应标准(如EN287 和EN288,或ASME IX)的操作人员和操作规程来完成和检验。因为非滑移式机械密封结构中的金属波纹管的焊接采用一般焊接标准或工业标准中所没有包括的专门的焊接规程,所以其焊接无上述要求。
6.1.6.10.2 制造商负责检查所有焊缝,确保它们采用正确的方式进行热处理和无损检测,并符合有效的规程。修复焊缝应采用相同的方法进行无损检测,以探测出原始缺陷。至少应对不锈钢零件进行渗透检测,对黑色金属材料进行磁粉检测。
6.1.6.10.3 除非另有规定,否则不承压结构件的焊接,例如支撑板、不受压接管、防护套和控制面板的焊接,应遵循AWS D1.1 的要求。
6.1.6.10.4 锻造材料或锻造、铸造复合材料制成的压力腔应遵循如下a)~d)的要求。如果螺栓连接的密封腔是焊接结构,也需满足如下要求:
- a) 板边缘应按ASME VIII 分卷1UG-93(d)(3)标准中的要求进行磁粉检测和渗透检测。
- b) 在焊缝清根或修平之后,焊接处及附近区域要进行磁粉和渗透检测,在焊接热处理之后需要再检测一次。
- c) 承压元件的焊接,包括腔体与水平或垂直法兰的焊接都应是全焊透焊接。
- d) 焊接的承压部件(无论厚度为多少),焊接后应做热处理。
6.1.6.10.5 与承压部件相连接的焊缝应遵照以下规定:
- a) 除了6.1.6.10.1 所要求之外,如果说明,可对焊缝进行100%的射线检测、磁粉检测、超声检测或渗透检测。
- b) 焊接在合金钢承压元件上的辅助管道材料应与腔体材料具有相同的性能,或采用低碳奥氏体不锈钢。经过买方同意,也可以采用与腔体材料相容的其它材料。如果需要进行热处理,管道焊接应在热处理之前进行。
- c) 如果有规定,在进行制造之前,制造商应向买方提交焊接接头的设计方案,并征求其同意。所绘图纸内容应包括焊接结构设计、尺寸、规格、材料、焊接前后的热处理。
- d) 所有焊缝都需要根据EN13445 或ASME VIII 分卷1 UW-40 中规定的方法进行热处理。
6.1.6.11 低温工况
6.1.6.11.1 对于操作温度低于-30℃(-20℉)或其它低温的工况,钢材应符合6.1.6.11.2~6.1.6.11.6 的要求。
::: warning
注:可参见附录B.3。该附录包括橡胶的温度范围。
:::
6.1.6.11.2 为了避免脆性破坏,低温工况所采用的材料应该能够承受规范和其它规定要求的最低工作温度。买方与卖方应就必要预防措施达成一致协议。预防的情况可能发生在运行、维修、运输、安装、试车和试验过程中。
好的设计取决于如何选择制造方法、焊接步骤、承压元件的材料,应注意材料在低于某一临界温度时,会发生脆化的现象。一些标准中如ASME 锅炉和压力容器标准公布的金属材料的设计许用应力是在材料的最小拉伸特性的基础上得到的。有些标准不考虑沸腾材料、半镇静材料、镇静材料、热轧材料和规范化材料之间的区别,也不考虑这些材料是由细小还是由粗大的晶粒组成。卖方在选择用于-30℃(-20 ℉)~40℃(100℉)的材料时需小心谨慎。
6.1.6.11.3 除非承压钢件不在ASME VIII 分卷1 UHA-51 中所规定的情况之内,否则,所有应用于在最低设计金属温度低于-30℃(-20℉)工况的承压件的基体和焊缝都需要进行V 形缺口冲击试验。冲击试验的结果要满足ASME VIII 分卷1 UG-84 的要求。
6.1.6.11.4 应用于最低设计金属温度为-30℃(-20℉)~40℃(100℉)工况下的碳钢和低合金钢承压零部件需要进行冲击试验,其要求如下:
- a) 承压件的主体厚度参见6.1.6.11.5 小于或等于25mm(1in)时,不需要进行冲击试验。
- b) 承压件主体厚度大于25mm(1in) 时( 参见6.1.6.11.5) ,免除冲击试验应符合ASME VIII 分卷1UCS-66.1.。免除冲击试验的承压件的最低设计金属温度可根据ASME VIII 分卷1 中图UCS-66.1 减少。如果材料不能免除冲击试验, V 形缺口冲击试验的试验结果应满足ASME VIII 分卷1 UG-84 的最低冲击功要求。
6.1.6.11.5 用于确定冲击试验要求的试验件主体厚度应大于如下值:
- a) 最大对接焊缝的名义厚度。
- b) 承压件的最大名义厚度,但不包括如下厚度:
-- 1) 结构支撑部分厚度,如支座厚度、拉筋厚度;
-- 2) 附加的结构件或者机械元件厚度,如夹套或密封腔厚度。
- c) 法兰名义厚度的四分之一,包括密封端盖厚度和密封腔法兰厚度。
6.1.6.11.6 买方应指定用于确定冲击试验要求的最低设计金属温度。
::: warning
注:通常最低设计金属温度是最低大气温度和最低输送液体温度的较小值。但是买方也可根据泵的工作特性(如减压时的自动制冷性能)指定最低设计金属温度。
:::