10.3.1 概述
密封试验顺序如图27 所示。
==图27 密封试验顺序==
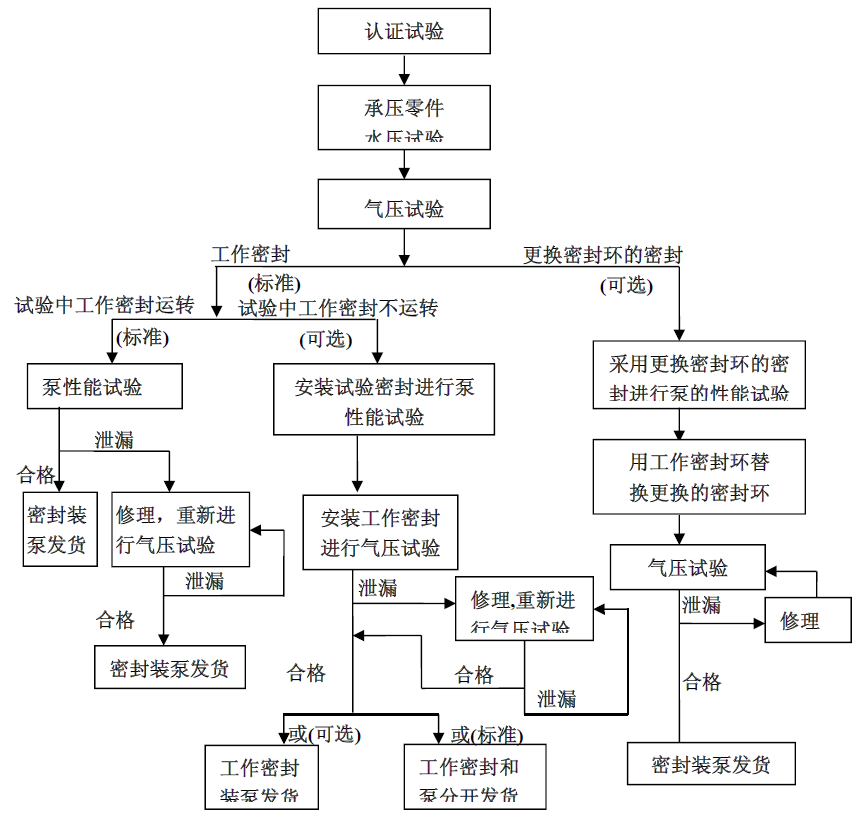
10.3.2 密封认证试验
10.3.2.1 目的
10.3.2.1.1 为了让密封件的最终用户对产品持有高度的信赖,相信所提供的特定型号密封的性能符合本国际标准的要求。每种密封类型及其辅助(支持)系统在投放市场前,须由密封制造商根据附录I 进行适当的认证试验,认证试验并不代表验收试验。认证试验的目的不是要对所有规格的每个密封逐一在所有测试液体中进行试验,而是模拟各种过程流体和典型设备操作类型,在特定流体介质中验证密封的结构和性能。
10.3.2.1.2 如果指定,经过密封件制造商和买方共同商定,可选用其他试验方案。在可实施的条件下,买方可以指定与标准试验不同的试验条件。
10.3.2.2 试验范围
10.3.2.2.1 密封的认证试验应由密封制造商根据附录I,在合适的试验台上进行。
10.3.2.2.2 为了试验指定的泵送流体,密封制造商的产品在合适的试验流体中应该能成功进行试验,详见表I.2.
::: warning
注:密封制造商的产品只需要对指定工况下的具有代表性的试验流体进行试验。没有必要在所有的试验流体中都进行试验,详见附录I。
:::
10.3.2.3 最低性能要求
10.3.2.3.1 除非另有规定要满足当地更高要求的排放法规,否则,应当按照如附录I.4.2,I.4.3,I.4.4 和I.4.9 对单端面密封进行试验,允许泄漏率规定如下:
- a) 采用EPA21 方法时,蒸汽浓度应小于1000 ml/m3(ppm vol);
- b) 每对端面的平均液体泄漏率应小于5.6g/h。
::: warning
注1:所有的机械密封都需要对端面进行润滑,以保证密封可靠运行,并希望泄漏率尽可能小。当水泵安装湿式接触密封(1CW),在泵用水进行泵性能试验时,泄漏液一般会蒸发而不可见。但是,当泵采用特殊端面结构时(如槽、台及波度等),可能导致泄漏率增加,而出现可见的液滴(见F.1.1)。有时双端面湿接触密封(3CW)在采用非蒸发性的润滑油和隔离液时,也可能产生液滴型式的可见泄漏,但泄漏率须小于5.6 g/h(每
分钟两滴)。
注2:密封买方应确定密封在将要使用场合下泄漏率的上限,并把这些限度和认证试验中的泄漏率数值相比较。当地法规规定的限度有可能要比上述规定的泄漏率数值要小。如果布置方式1 密封不能满足当地对排放或泄漏的限制规定,那么可能需要采用布置方式2 或3 密封来满足这些使用限制要求。
:::
10.3.2.3.2 除非另有规定要满足当地更高要求的排放法规,当抑制密封按附录I.4.5 步骤进行试验时,最大容许泄漏蒸汽浓度按EPA21 方法应小于1000 ml/m3(1000 ppm vol)。
10.3.2.3.3 在认证试验完成后,密封端面的总磨损率不能超过密封端面有效磨损高度的1%。
::: warning
注1:如果单端面密封在认证试验中磨损过度,这就可能意味着该使用条件选用双端面密封会更好。
注2:密封尺寸、转速、压力和液体的不同,密封端面的磨损也不同,而且不成线性变化。大部分密封端面的磨损出现在启动开始或启动之后很短的时间内。
:::
10.3.2.4 试验结果
密封制造商应根据附录E 的要求,进行认证试验和提供认证试验结果。认证试验结果至少应包含图I.9或图I.10 的内容。凡观察到的任何会导致密封不能满足本国际标准对可靠性和性能要求的情形都应报告。
10.3.3 机械密封承压元件及附件的水压试验
10.3.3.1 除了由整个锻件或棒料加工而成的密封端盖,密封承压壳体元件都须用进行水压试验,试验压力最少应为最大允许工作压力的1.5 倍,但不得低于0.14MPa (1.4bar) (20 lb/in2)表压。试验液体的温度应高于试验材料的零韧性转变温度。
10.3.3.2 如果承压元件在工作温度下的材料强度低于室温下的材料强度,那么水压试验压力应乘一个系数,这个系数等于材料在室温下的许用应力除以材料在工作温度下的许用应力。所使用的许用应力,对于管道符合ASME B31.3 规定,对于容器应符合EN 13445 或ASME Ⅷ第1 分篇规定。这样求得的压力就是进行水压试验的最低压力。机械密封数据表(见附录C)上应注明实际的水压试验压力。
10.3.3.3 如果可以,试验应符合EN 13445 或ASME Ⅷ的要求。如果此规范的试验压力和本标准的试验压力不一致,则采用压力较高者。
10.3.3.4 奥氏体不锈钢水压试验用的液体,其氯化物含量不应超过50mg/kg(50 ppm wt)。为了避免由于蒸发干燥而导致氯化物的沉积,在试验完成之后应该将试验部件上的残留液体全部除去。
10.3.3.5 试验时间应足够长,以便在试验压力下对零件进行全面的试验。如果至少30 分钟以后密封腔没有泄漏也无渗漏,则水压试验即为合格。
10.3.4 密封制造商对工作密封进行试验
10.3.4.1 在机械密封最终装配完成后,密封制造商需按照10.3.5 的要求采用空气对每个密封进行气压试验,应符合下列a)条至c)条的要求:
- a) 密封在装配时需经过全面检验、清洗、核实端面上没有润滑油脂。并核对密封的型式、尺寸、材料和垫片、零件编号。
- b) 试验设备应能适应整套集装密封,不需要修改密封元件、密封腔(如果制造商提供)或密封端盖。
- c) 可对布置方式2 或3 密封中的每个密封端面进行单独试验。
10.3.4.2 气压试验成功完成之后,经过试验的集装密封不应该拆开,在集装密封上贴上“密封制造厂气压试验合格”字样的标签,注明试验日期和检验人员的姓名。
10.3.4.3 如果密封没有通过气压试验,整个试验过程需重复进行,直到试验成功。
10.3.5 装配完整性试验
10.3.5.1 目的
10.3.5.1.1 为了让买方更好的确认密封制造商的密封已经正确的装配,每一个新的或者维修过的集装密封,在发货前都应该由密封制造商按照10.3.5 步骤采用空气或者氮气进行气压试验。完整性试验是一个验收试验。
::: warning
注:装配完整性试验是为了说明密封件已经正确的装配在一起。密封制造商并不希望密封一点不漏,详见A.1.3 中。多年的经验表明低压试验对密封是有利的。密封装配完整性试验结果并不能代表密封在实际工况流体中的性能。
:::
10.3.5.1.2 如果指定,应该由密封制造商和买方相互协商选择空气或者氮气进行气压试验。
10.3.5.2 装配完整性试验范围
10.3.5.2.1 密封完整性试验应由密封制造商根据10.3.5.2.2~10.3.5.2.5,在合适的试验台上进行。
::: warning
注:通常情况下,在试验台上用一个筒体模拟较大的密封腔,筒体上具有不同的连接结构,螺栓,阀门和仪表,并使用连接盘来满足不同尺寸的密封。
:::
10.3.5.2.2 试验台应具有各种连接尺寸,可以按照10.3.5.3 来独立地模拟密封腔,缓冲腔,缓冲腔或抑制密封腔。
10.3.5.2.3 试验台须有一个加注液体和加压系统,该系统可以从正在试验的模拟密封腔,缓冲腔,缓冲腔或密闭腔隔离开来。
10.3.5.2.4 在任何腔室中,用于进行加压和试验的气体体积最大为28L(1 ft3)。
10.3.5.2.5 用于试验的压力表要有一定量程范围,并且应使0.17MPa (1.7 bar) (25 lb/in2)[表压]位于全量程中间位置附近。
10.3.5.3 装配完整性试验过程
10.3.5.3.1 每个模拟的密封腔,隔离或缓冲腔和密闭的腔室都应该单独地充入洁净的空气,加压到0.17MPa (1.7 bar) (25 lb/in2) (表压)。
10.3.5.3.2 根据10.3.5.3.1 加压后,把密封腔,隔离腔,缓冲腔和密闭的腔室与压力源的通路切断,保压最少5min。
10.3.5.4 装配完整性试验的最小性能要求
10.3.5.4.1 根据10.3.5.3 试验中最大压降应为0.014MPa (0.14 bar) (2 lb/in2)。
::: warning
注1:压力降与被试验腔室体积成反比。如果试验腔室内所包含的气体体积非常小,需要慎重考虑。当试验非接触式密封时,同时试验两套核心密封组件,或者现场试验气体体积非常小的双端面密封,可能使用特殊的密封试验条件或者验收标准。例如,同时采用两套核心密封件或气体体积非常小的双端面密封进行装配完整性试验时可能超出10.3.5.4.1 的标准范围的规定,但是实际操作工况下密封却可以良好地工作。
注2:由于安装后的体积和安装对中的变化,密封完整性试验不能重复进行。
:::
10.3.6 泵制造商对工作密封进行试验
10.3.6.1 更换密封环的密封
如果指定,把采用更换密封环并经过气压试验合格的密封送往泵制造商,以进行泵的性能试验。泵性能试验完成之后,须将工作密封环装进密封内并根据10.3.5 进行气压试验。
10.3.6.2 泵性能试验中,密封不运转
如果指定,为了避免损坏工作密封,在泵性能试验中工作密封不运转。在进行泵性能试验的时候,使用泵制造商提供的试验密封。当泵性能试验完成后,安装密封制造商提供的工作密封和密封腔(如果提供),再根据10.3.5 进行气压试验。如果发货时泵上没有安装工作密封,须注明。